2018 CEOs Who "Get It"

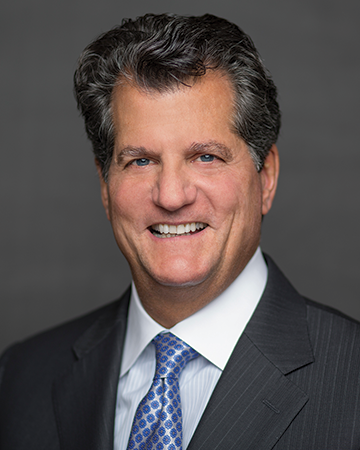
Chris Pappas
President and CEO
Trinseo
Berwyn, PA
Trinseo is a global materials company that develops and produces plastics, latex binders and synthetic rubber that drive the creation and manufacture of goods within multiple high-growth end-markets. The company has 2,200 employees.
Describe your personal journey to becoming a CEO who “gets it.” What experiences or lessons brought you to where you are now?
The chemical industry has yielded so many wonders that are essential to modern life, but like many industrial businesses, the raw materials and manufacturing processes we use have risk. It takes care every day to make sure we are operating safely and responsibly.
Throughout my career, I’ve been blessed to work at companies that take safety seriously, but any good leader will tell you that safety doesn’t happen organically or arise solely from good intentions. For me, focusing the organization on safety is a relatively simple concept – it’s about establishing a culture where caring for your co-worker, for your community, and for yourself and your family are just a way of everyday thinking.
When Trinseo was carved out of Dow Chemical in 2010, we really didn’t have a company, just a collection of businesses and assets. We had to work hard to build a company and corporate culture – one with safety and sustainability always at the core of what we were trying to accomplish.
At all levels, we ask a lot of our people in terms of accountability and leadership, and in return we want everyone to feel that their health and safety will never be put at risk. Right from the very founding of Trinseo, we said, “If a job cannot be done safely, it should not be done,” and we empower every employee to stop work if they have a concern. We make sure that safety is discussed at every leadership meeting, and we have a “vision of zero” for workplace injuries and environmental incidents.
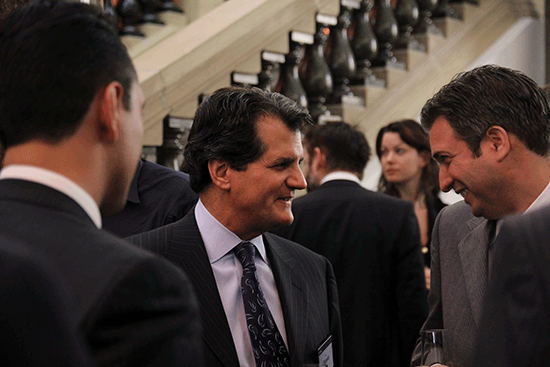
Why is safety a core value at your organization?
I believe this commitment to safety is at the center of our success and our growth. It has helped us retain top talent and find the best workers across the globe.
When we were carved out of Dow Chemical, we made a conscious decision to maintain our strong heritage and history of engineering excellence, safety process discipline, and a relentless continuous-improvement mindset. And we decided to pair that with new traits as a young company, like an open and collaborative culture.
We treat safety performance as a line management responsibility, with each line manager being accountable for the safety results of their department. We expect all leaders to show a strong and visible commitment to safety. Safety also is a critical piece of career advancement for leaders in manufacturing. Simply put, if a production leader or operations leader has consistently poor safety performance in their plant, this can affect their promotions and career advancement in the future.
We’ve found that safe and healthy working environments foster greater productivity, but also strengthen our relationships in the communities where we operate and bring us closer together as an organization.
The most valuable resources we have at Trinseo are our employees. Keeping our people safe and healthy is essential to our success and all that we’ve been able to accomplish.
What is the biggest obstacle to safety at your organization, and how do you work to overcome it?
Our safety performance is very good, with an OSHA recordable rate of between .27 and .32 each year, including contractors. We want to keep getting better in order to get to our vision of zero incidents, but our injury has more or less plateaued over the last several years.
In order to get better, we need to focus on behavior. And we know that many of our incidents have a behavioral component. So in 2016, we started working on redesigning our behavioral safety program, and launched it in early 2017 under the name “Safety on Purpose.” This is a real shift for us because we’ve historically focused on engineering solutions to reduce the risk of what we do, and not always focused as much on the behavioral component. So we completely redesigned our behavioral safety program, using ideas we gained from benchmarking other leading companies, combined with expertise from a consultant.
The Safety on Purpose program was previewed at a leadership meeting in October 2016, followed by full launch in Spring 2017 via 22 training sessions across all of our manufacturing plants. The core training is 18 hours, aimed at each plant’s leadership. We call these people “safety influencers,” and we have trained over 200 of them. In addition, the plant leader introduces the program in several shorter sessions to everyone who works at the plant, including contractors. Over 1,000 people have received this one-hour introduction to the program, to get them engaged in safety conversations. We decided to deliver that training in local language because we found this program works much better when employees can feel comfortable expressing themselves and asking questions in their native tongue.
It will take time, but we feel confident that improving behavior will help us get to that next level and ultimately our vision of zero incidents.
How do you instill a sense of safety in employees on an ongoing basis?
It’s built on the belief that safety doesn’t happen by itself, or even with good intentions and superior engineering. Safe workplaces arise from commitments by every employee to embed safe behaviors in everything they do, coupled with strong programs, operating discipline and highly trained people in our organization.
It starts with tone at the top. I begin each biweekly leadership meeting with a report on our EHS performance. So it’s front and center not just for leaders in manufacturing, but for leaders in every other department, too.
How does your organization measure safety? What are the leading indicators that show you how safe your organization is, and where do you see room for improvement?
Our long-range goal is to be incident free – an important metric that we achieved from April 2016 through January 2017. And many of our plants have gone more than a year incident-free. We celebrate this each year with our Triple Zero Awards, which are given to each plant site that has zero injuries, zero spills and zero process safety incidents in a calendar year. Typically, well more than half our plants have a Triple Zero year.
At the company level, each January we establish an EH&S dashboard, with annual targets for injuries, spills and process safety incidents. And everyone has a personal stake in it because each employee in the company has a small part of their annual bonus tied to these EH&S targets.
In terms of opportunity for improvement, there are always things we can do to get better. For 2018, our focus will be to continue to drive full adoption of our behavioral safety program “Safety on Purpose,” and to implement computer-based training with video scenarios for life-critical standards. Zero incidents is our vision, and we believe we can get there.
Post a comment to this article
Safety+Health welcomes comments that promote respectful dialogue. Please stay on topic. Comments that contain personal attacks, profanity or abusive language – or those aggressively promoting products or services – will be removed. We reserve the right to determine which comments violate our comment policy. (Anonymous comments are welcome; merely skip the “name” field in the comment box. An email address is required but will not be included with your comment.)