‘Train and practice’
How to mitigate common forklift hazards
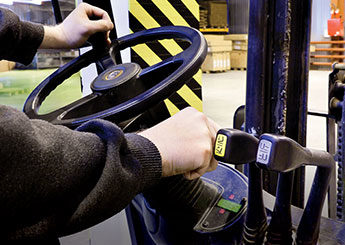
KEY POINTS
- Forklift operators should not assume that all workers on foot can see them, and vice versa.
- Use electric forklifts instead of gas or propane models when working indoors to avoid carbon monoxide poisoning.
- Forklifts can easily hit upright shelving in a warehouse, resulting in serious damage that could cause the shelf to collapse and injure workers – sometimes months later.
Powered industrial trucks, also known as forklifts or lift trucks, make lifting and transporting heavy objects easier in the workplace. However, this advantage also comes with risk if a forklift is operated unsafely or by an untrained driver.
OSHA’s Powered Industrial Trucks Standard (1910.178) was the sixth most cited standard in fiscal year 2012. According to the Bureau of Labor Statistics, approximately 90 workers died from injuries related to forklifts, order pickers and platform trucks in 2011.
Experts say following best practices and maintaining situational awareness can help prevent forklift-related incidents.
Training
Lack of training is one of the most common OSHA citations related to forklifts, according to Tim Neubauer, senior consultant at the National Safety Council.
Neubauer, who was a safety director in general industry and construction and has driven forklifts, said many people believe that if they can drive a car, they can operate a forklift. However, forklifts differ greatly from cars. One major difference, Neubauer said, is that motor vehicles have four points of suspension while forklifts have three. This means they can tip over easily. Also: Unlike cars and trucks, which steer from the front, forklifts steer from the rear – meaning the steering wheel turns the back wheels.
“If you don’t train and practice, and it’s not in your mindset, you will turn the wheel and the rear end swings and it crashes into something,” Neubauer said.
OSHA prohibits workers younger than 18 from operating forklifts, and requires operators to be properly trained and authorized by their employer. However, what often happens, Neubauer said, is that employers authorize workers without training them, or a worker receives some training and operates the forklift without the employer’s knowledge. Both scenarios are problematic.
Neubauer emphasized the importance of providing training that is specific to the forklift the worker will be operating. Some workers have the mindset that if they can drive one type of lift truck, then they can drive all types. “That is a very big mistake,” he said.
Inspections and workers on foot
OSHA requires forklift operators to perform a pre-shift inspection, during which they are supposed to check fluid levels, tire conditions, safety devices and the condition of the forklift. Eric Wiseman, safety compliance supervisor at the Washington State Department of Labor and Industries, said inspections go hand in hand with the operator having the authority to choose not to operate a forklift if it appears unsafe.
“First and foremost, I look at training programs to ensure that the operators are instilled with a sense of 100 percent accountability for control of the forklift,” Wiseman said. “The operator should have 100 percent authority to stop at any time when they’re uncomfortable in the operation of it.”
Also important is a sense of vigilance about keeping nearby workers safe. Wiseman said the operator should look before backing up, and workers should stay clear of the forklift and the toppling radius of the load it is carrying. That includes not walking under or even near an elevated load.
However, both drivers and workers on foot often take their visibility for granted. Wiseman described a typical scenario. “‘As I was backing up, I assumed he knew I was there because of the noise and the smell of the forklift’ – that’s what you hear from the forklift operator,” he said, adding that a typical passer-by’s response is, ‘I thought he saw me, and he should be more careful with his forklift.’”
The load
Before making any modifications to a forklift, including using an attachment, employers should receive written permission from the manufacturer. Wiseman pointed out that personnel lift attachments can create additional hazards, such as hitting overhead structures.
If an operator needs another employee to help with a large load, Wiseman advises workers to “ensure they never touch the load but instead use a long tagline and stay clear of the toppling radius and path of travel.” Other recommendations include discussing the task beforehand and assigning a spotter to oversee it.
Neubauer said unauthorized workers should be kept away from forklift activity, and operators should never pick up another person with the forks of the forklift. He said it is quite common – and unsafe – for someone to stand on the forks to reach a shelf or change a lightbulb.
Even when a load has been dropped off, danger exists. When driving an unloaded forklift, the best practice is to keep the forks as low to the ground as possible, Neubauer advised.
In transit
Forklift operators need to avoid distractions. Neubauer used the example of an employee who was texting while operating a forklift and struck another lift truck, causing it to tip over.
In addition, forklifts can encounter a variety of hazards while moving. Inadvertently hitting a pothole in a parking lot can cause a tip-over. Forklift operators should watch out for steep inclines or drops and avoid traveling too fast.
Extra caution is required on loading docks. “It’s very easy to drive a forklift off a loading dock by losing situational awareness,” Wiseman said. He emphasized the need to wear the forklift’s safety belt and know what to do in the event of a tip-over.
If a forklift is tipping over, OSHA recommends that you do not attempt to jump off. Grip the steering wheel tightly, brace your feet, and lean forward and away from the impact.
Indoor hazards
Carbon monoxide poisoning is a major concern when gas- or propane-powered forklifts are used indoors. Inhaling too much of the odorless, colorless and tasteless gas can lead to loss of consciousness – and even death. Although proper ventilation and carbon monoxide alarms can help, Neubauer recommends using electric forklifts, which do not produce carbon monoxide. He noted that caution should be used even in structures that are partially open to the outdoors.
Another indoor workplace issue is shelving. A forklift can easily scrape a shelf in a cramped warehouse. Even if the resulting dent is small, the damage could be severe.
“The slightest little kink in upright shelving can cause a shelf to collapse,” Wiseman said. His recommendation is to inspect all four corners and look for damage, and have a professional engineer verify that dented shelving can still hold the intended weight. Otherwise, the compromised shelf could give way months later, and the shelf’s contents could fall on a worker or cause tripping hazards.
Be clear about safety
Employers should think about the message they send with their directions to the forklift operator, Wiseman said. Setting an unrealistic deadline may cause the operator to rush. Also, saying “Hurry up and get this done by 2:00 – and oh, by the way, be safe” makes safety an afterthought.
When that happens, “the employers with the best of intent can inadvertently send a mixed signal to the operators,” Wiseman said, adding that the better approach is to emphasize that safe operation takes priority over production.
Post a comment to this article
Safety+Health welcomes comments that promote respectful dialogue. Please stay on topic. Comments that contain personal attacks, profanity or abusive language – or those aggressively promoting products or services – will be removed. We reserve the right to determine which comments violate our comment policy. (Anonymous comments are welcome; merely skip the “name” field in the comment box. An email address is required but will not be included with your comment.)