Safety Leadership: Putting safety leadership in the path of supervisors’ work
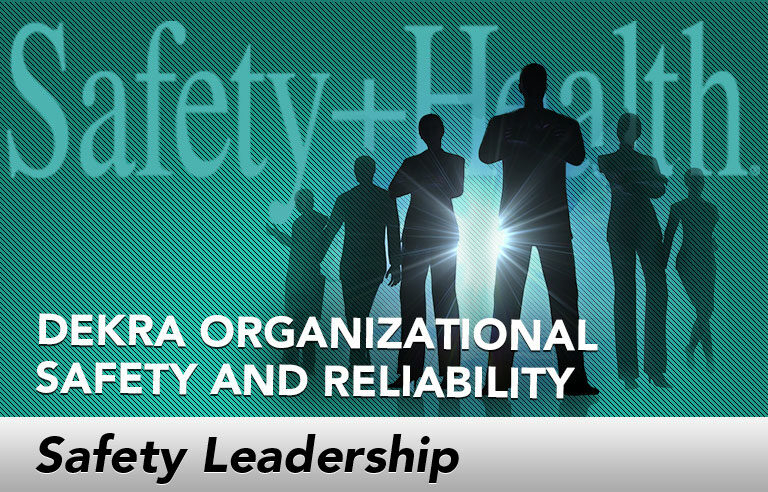
Editor’s Note: Achieving and sustaining an injury-free workplace demands strong leadership. In this monthly column, experts from global consulting firm DEKRA Insight share their point of view on what leaders need to know to guide their organizations to achieve world-class safety performance.
This column originally ran in the February 2013 issue of Safety+Health.
Great safety leaders change the culture for the better, but how they impact culture change depends on a leader’s unique role. For front-line supervisors and managers, becoming a great safety leader is a special challenge. They occupy roles that are highly tactical compared to their colleagues at other levels. At the same time, their closeness to individual team members means they communicate the intentions and values of the organization in a way that no other leader can.
For years, organizations have tried to help front-line leaders leverage their position for safety improvement by adding on to existing priorities and demands. The results are usually the same: good intentions that seldom survive daily realities. Today, some organizations are taking a lesson from lean manufacturing and embedding safety leadership opportunities into the path of the supervisors’ work. In other words, innovative safety leaders use the interactions they are already having with their employees to talk about ways to manage and control exposures.
Moments of truth
In customer service, a moment of truth is an instance of contact between a customer and a company that provides an opportunity to form a meaningful impression on the customer. In safety, moments of truth occur when supervisors communicate with workers about safety. How supervisors approach opportunities; what they focus on, ignore and choose to emphasize; and what they delegate to others all have a powerful impact on site safety. Effectively taking advantage of these instances can profoundly strengthen safety culture and lead to lasting improvement in safety performance. There are five chief activities (or leverage points) that supervisors can leverage to shape their organization’s safety culture:
- Safety contacts. Any instance of communication between a supervisor and a direct report focused on safety is an opportunity to communicate organizational value for safety.
- Job safety briefs. Meetings that are conducted before, during or after the job and focus on identifying ways to mitigate hazards, and planning the safest way to approach a task, set a practical standard for safe work. Supervisors need to be able to conduct briefs as an engaging, two-way discussion; ensure workers understand what is being decided before work resumes; and follow through on actions and responsibilities.
- Lifesaving procedures: application and verification. Well-meaning employees can inadvertently develop dangerous shortcuts when trying to balance procedures with efficiency. The only way for supervisors to know if hazards are arising is to personally check. This means supervisors must go into the field and directly verify the real-life application of these procedures to ensure they are being done properly.
- Physical hazard identification. Even if workers are practicing safe behaviors and doing everything correctly, they still may be at risk from a hazard without realizing it. Supervisors can mitigate this by broadening their visual scan beyond workers’ actions to look for potential exposures in surrounding conditions and equipment.
- Incident response and root cause analysis. How supervisors handle incident response and analysis says a lot to workers. When an incident occurs, supervisors must respond immediately to care for the worker and take mitigating steps to address exposures. Supervisors must know how to ask the right questions to understand the root cause of an incident and establish and implement a successful plan of action. Done effectively, this activity can have an immediate and positive impact on employee participation in safety efforts.
Sharpening the focus
Sometimes less is more. By sharpening our focus on only a few important safety activities, supervisors can better separate the wheat from the chaff of their daily requirements and directly engage the safety issues that are most critical. This is not to say these activities are easy to do. But with leadership support, the right focus, conviction and consistent application, supervisors who do these activities help create significant and lasting change in both safety performance and the organization’s overall culture.
A vice president at DEKRA Insight, Michael Hajaistron helps leaders in mining and other high-risk industries develop organizational cultures that achieve safety, business and profit objectives.
Post a comment to this article
Safety+Health welcomes comments that promote respectful dialogue. Please stay on topic. Comments that contain personal attacks, profanity or abusive language – or those aggressively promoting products or services – will be removed. We reserve the right to determine which comments violate our comment policy. (Anonymous comments are welcome; merely skip the “name” field in the comment box. An email address is required but will not be included with your comment.)