Safety Leadership: Applying behavior-based safety to serious and fatal injury prevention
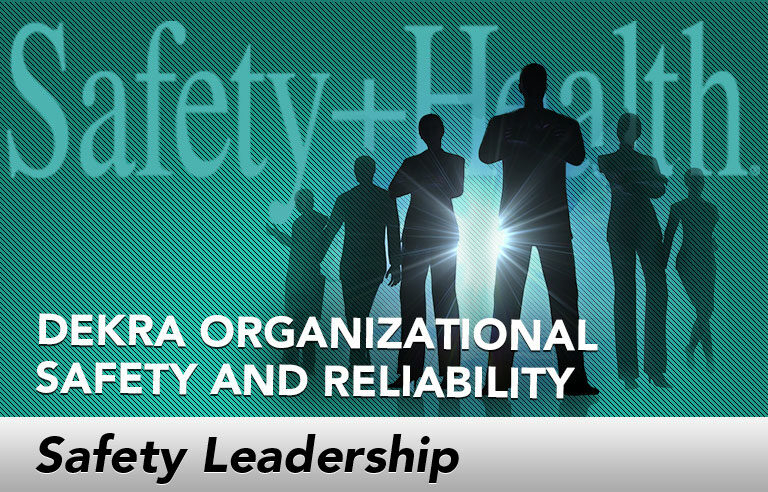
Editor’s Note: Achieving and sustaining an injury-free workplace demands strong leadership. In this monthly column, experts from Ojai, CA-based consulting firm BST share their point of view on what leaders need to know to guide their organizations to safety excellence.
Sometimes the best tool for a complex problem can be right in front of us. But does that principle apply in the case of something as complex and urgent as a serious injury or fatality (SIF)? For years, organizations have sought to understand the growing gap between incident rates that have steadily declined across industry and fatality rates that have not. The answers have challenged the conventional wisdom on accident causation.
For instance, research shows that the discrepancy between fatal and less-severe injury outcomes is due in part to leaders and safety practitioners treating all incidents the same, when in reality roughly 20 percent of incidents have the potential to be an SIF. As a result, many organizations are now paying increased attention to the potential severity of their incidents, first aids and near misses.
Given our new understanding, what practical steps can leaders take to reduce their exposure to potential SIF incidents?
Adapting a proven system
A mature and high-functioning behavior-based safety process has proven to be an effective tool for reducing overall incidents in many organizations. However, a typical BBS observation does not probe deep enough to discover and document SIF exposures. Can this process be modified and leveraged to identify the precursors, pre-conditions and exposures that lead to SIF incidents before they occur?
To answer this question, my colleagues recently undertook a study of 55 SIF and SIF-potential cases. They sought to determine if the precursors, pre-conditions and exposures that contributed to the occurrence of these incidents would be discoverable through discussions, interviews and/or observations. This examination was done by two safety experts and SIF experts working independently. Analysis of the results indicates the raters were in high agreement with each other and that 48 of the 55 cases (87 percent) could have been detected through an observation and interview process.
This is an encouraging discovery. However, leveraging BBS processes to detect SIF precursors and exposures is not as simple as it sounds. At a minimum, it involves leaders ensuring the following steps:
- Align observation sheets with SIF exposures. In many potential SIF incidents, the worker is engaged in a high-risk situation (such as working at heights) in which management controls are inadequate, missing or not complied with. Therefore, observation sheets must include not only behaviors, but also conditions and management controls.
- Give your observers specialty training. In high-functioning BBS processes, observers are trained on safe and at-risk behaviors and how to give feedback. For SIF-potential observations, additional training is necessary to observe for high-risk situations and to be able to effectively interview the worker on the exposures and management controls.
- Identify the right observers. The ability to interview effectively (set the worker at ease, ask open questions, follow up on missing or inconsistent information, etc.) is not necessarily inherent in BBS observers. Therefore, care must be given to identifying the right observers for enhanced SIF observation/interview training. This may also involve training supervisors, managers and safety professionals.
- Analyze and take action on data. Results from observations and interviews need to be captured and analyzed for trends and ongoing exposures. Leaders then need to take prompt action to address the individual and systemic issues that elevate the SIF-potential risk.
Although not all potential SIF incidents can be identified using this process, we have evidence that suggests that a great many of them can be detected ahead of time and the exposure can be mitigated before it becomes a serious injury or fatality.
This article represents the views of the author and should not be construed as a National Safety Council endorsement.
Michael Mangan, Ph.D., is vice president, research and development for BST. His work helps organizations understand performance and design interventions for improvement.
Post a comment to this article
Safety+Health welcomes comments that promote respectful dialogue. Please stay on topic. Comments that contain personal attacks, profanity or abusive language – or those aggressively promoting products or services – will be removed. We reserve the right to determine which comments violate our comment policy. (Anonymous comments are welcome; merely skip the “name” field in the comment box. An email address is required but will not be included with your comment.)