My Story: Stephen Thompson

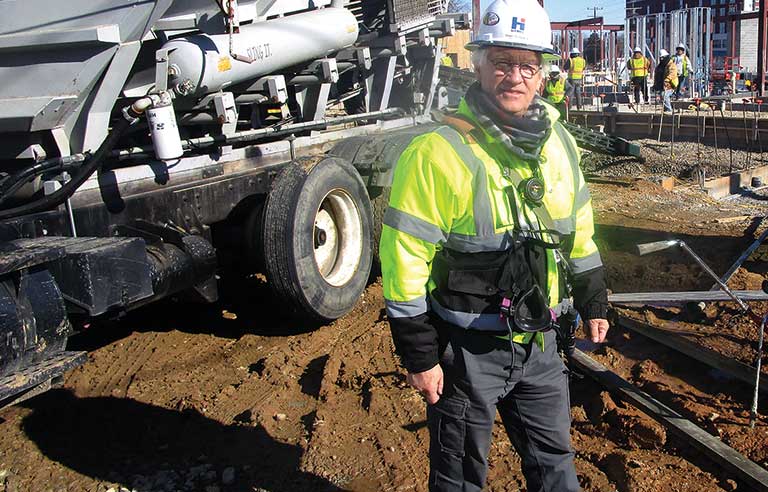
My story spans 50 years in the construction trade. It began in 1969, when I was working as a laborer in the industry. I was exposed to multiple work-related duties with hazards ranging from unprotected trenches to various harmful dusts without respiration protection. This experience helped me recognize the need for addressing unsafe work habits and determining how these tasks could be done safely.
Until 1970, employers were not versed in safe, compliant work habits. I was seeing a lack of work ethic and varied skill levels: Ask two carpenters to hammer in a nail and the first one would do it skillfully and the second one haphazardly; the second worker usually would be injured in the process. I was determined to improve their personal safety and well-being. As a superintendent, I felt responsible to take on the challenge.
OSHA was created in the 1970s, safety standards were developed and then safety inspections followed. These reinforced the importance for employers to train their workers. The enforcement technique from a third-party safety company was not effective, the employer could not be fined from the inspection and the safety inspector did not follow up.
After several years of not achieving an acceptable safety culture – and paying significant OSHA fines – my current company asked me to head up an internal safety department. To improve my credibility, I began taking safety-related courses and safety trainings at trade centers. I became an OSHA trainer through the Chesapeake Region Safety Council and took numerous other occupational safety and health disciplines. I then passed the ASP exam to become an Associate Safety Professional.
I continued my studies for four more years at the Community College of Baltimore County to achieve a degree in occupational safety and health technology. My enhanced knowledge was necessary to enforce compliance with authority. In this business, you need to be right all the time. Reputation develops respect. I eventually developed a division in the company, CSI: Corporate Safety and Investigation. It inspects five points of safety and health: OSHA compliance, driver improvement, loss management, quality control and employee well-being.
These disciplines are enforced by a quarterly point system of accountability for each site. Starting with 1,000 points, a site is inspected and given points for compliance or deductions for noncompliance – to be credited back if corrective actions are returned to the CSI office.
Eventually, I became known and respected as “Safety Steve.” My efforts have made the company’s program known and respected by all subcontractors and outside agencies that have business with us. I became the one to go to when there was a question about an unsafe condition or how to work safely to avoid a hazardous condition. Now, site safety inspections are embraced by workers, because they know that I am looking out for their best interests and will do what it takes to protect and assist them in maintaining their well-being.
My experience has allowed me to recognize the safety issues at hand and evaluate compliance. I can smell the dust on the floor and tell if it is fresh and then observe to see how it got there. A leaning stepladder, a bad cord, a short ladder – all develop into a scenario of non-compliance. The acceptance of the thousands of workers I have met has made this second career fulfilling, and I am proud of the amount of work it took to get here.
Stephen Thompson, ASP
Corporate Safety Officer
lkridge, MD
Post a comment to this article
Safety+Health welcomes comments that promote respectful dialogue. Please stay on topic. Comments that contain personal attacks, profanity or abusive language – or those aggressively promoting products or services – will be removed. We reserve the right to determine which comments violate our comment policy. (Anonymous comments are welcome; merely skip the “name” field in the comment box. An email address is required but will not be included with your comment.)