Safety Leadership: Why understanding brain-centered hazards matters for warehouse work
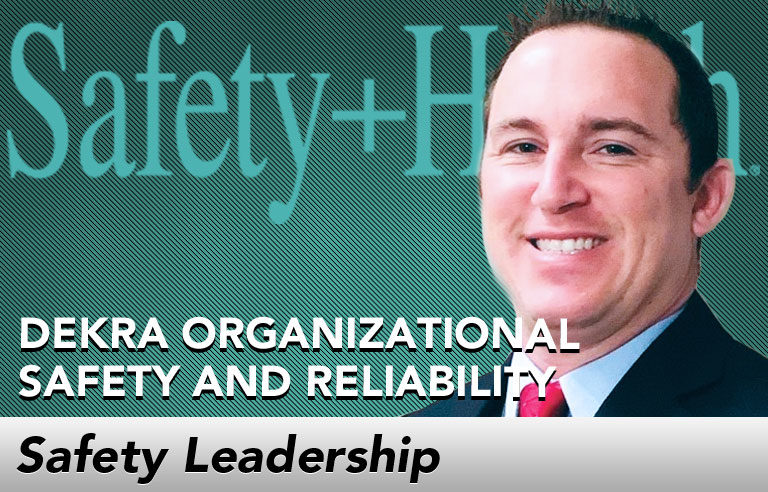
Editor’s Note: Achieving and sustaining an injury-free workplace demands strong leadership. In this monthly column, experts from global consulting firm DEKRA Organizational Safety and Reliability share their point of view on what leaders need to know to guide their organizations to safety excellence.
Imagine you’re operating a powered industrial truck in a 1 million-square-foot facility. Surrounding you are long aisles with racks on either side stacked with product. You follow a rigorous pick schedule. One route weaves you up and down aisles and then spits you to a “T” intersection, where product is stacked on the floor. Diagonal from the intersection is a massive support beam with a bright yellow bumper around the base. For weeks, product has built up around this beam, shielding it from view. The boxes are now on the edge of the aisle and provide the visual that directs drivers where to travel.
One day the boxes are moved, exposing the beam. After navigating the usual maze of aisles and picking product, you find yourself at the familiar intersection. You stop and look both ways, then accelerate to the far side of the aisle to the next pick location. As you accelerate, you hit the beam. The truck abruptly halts and product topples off. Worse, you propel face-first into the grating of the front windshield.
In real life, the operator escaped serious injury with only a few bumps and lacerations, yet the incident could have been much worse.
So what happened? How does a veteran operator miss such an obvious exposure? The answer is in our brain. One part of our brain that supports information processing is the cerebrum. It handles our decision-making and conscious, analytical thinking. We call this the “slow brain,” as it takes more time to activate behavior.
The other part of our brain is the paleomammalian, and it activates reactive and habitual behavior. It’s commonly referred to as the “fast brain.” The fast brain isn’t ideal in industrial environments such as warehouses, where working the same task repeatedly can result in someone getting hurt.
The scenario above created a prime opportunity for the fast brain to go into action. The operator ran into the beam as the result of carrying out the task habitually, with limited conscious processing of updated information where a change in the environment went undetected.
In other words, the fast brain prevented him from becoming aware of the change in his environment and responding properly. Another key factor leading to human error in this incident has to do with visual recognition. The operator stated that he didn’t see the support. That’s because we see with our brain. The brain tells our eyes to search for information to process and activate behavior that best suits the situation. When our brain doesn’t identify something that is significantly new or different, it seeks to apply similar behavior to a familiar situation.
Fast-brain functioning and visual recognition are two examples of brain-centered hazards. These are hazards related to our neurological makeup and are responsible for human error. Brain-centered hazards affect all people, including experienced workers. It’s important to understand how these two hazards function and then design work environments and activities in a way that controls them.
Many organizations seek to “fix” the person after an incident in which human error was deemed a contributing factor. But brain-centered hazards reside in all people. That’s why it’s important to proactively identify where these reside in your workplace. Layers of protection can include:
- Providing visual cues highlighting changes in the work environment.
- Creating a forum to discuss pre-job safety briefs for specific tasks, as well as highlighting known changes that may add or change exposure.
- Rotating tasks to prompt more slow-brain functioning.
- Completing pre-task exposure assessments.
The way our brains are wired plays a key role in making work-related decisions that have significant safety implications. Understanding brain-centered hazards is imperative for any organization that wants to reduce the potential for human error. Minimizing human error is paramount for any organization that wants to reduce serious injuries and fatalities.
This article represents the views of the author and should not be construed as a National Safety Council endorsement.
Matt Hargrove is a principal consultant working in the Brain-Centric Reliability practice within DEKRA Organizational Safety & Reliability (dekra.us/osr). To learn more about Brain-Centric Reliability, go to dekra.us/en/organizational-safety-reliability/brain-centric-reliability.
Direct to your inbox: Sign up to be notified in email about new "Safety Leadership" columns.
Post a comment to this article
Safety+Health welcomes comments that promote respectful dialogue. Please stay on topic. Comments that contain personal attacks, profanity or abusive language – or those aggressively promoting products or services – will be removed. We reserve the right to determine which comments violate our comment policy. (Anonymous comments are welcome; merely skip the “name” field in the comment box. An email address is required but will not be included with your comment.)