Safety Leadership: Is your SIF prevention process missing something?
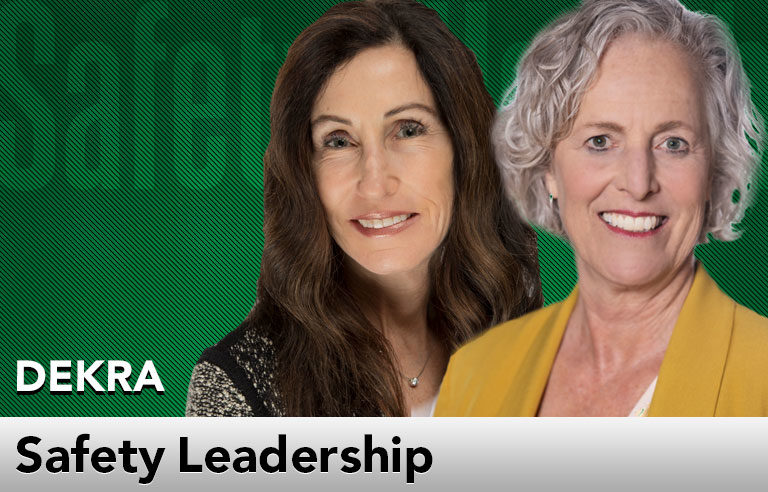
Editor’s Note: Achieving and sustaining an injury-free workplace demands strong leadership. In this monthly column, experts from global consulting firm DEKRA share their point of view on what leaders need to know to guide their organizations to safety excellence.
Preventing serious injuries and fatalities requires a targeted approach to reduce or eliminate serious exposures. Many organizations have begun developing a process to eliminate, control or reduce SIF exposures.
Whether you partner with experts or build your own SIF prevention process, ask yourself the following questions:
Are we using data to help inform decisions and actions?
It’s common for organizations to develop a sound classification system based on potential and analyze historical data that determines the most prevalent SIF exposures. Responding to incidents is essential, both for immediate control and root-cause analysis. Taking steps to use the data for decision-making and implementing actions to address the identified issues is often more complex. An effective investigation is crucial to developing the most efficient corrective actions to ensure the incident doesn’t repeat. This last step is important – and the one that many organizations struggle with.
Is our SIF prevention process fully integrated into our safety management system?
Your SIF prevention efforts shouldn’t be a standalone process. When beginning a SIF prevention process, it’s common to focus efforts on this element of your safety system. It’s easy to rally people to the cause of preventing significant harm. However, it’s crucial to integrate SIF prevention into the overall efforts to keep people free from harm. SIF prevention requires a narrow and deep approach to control and eliminate those exposures. We want to spend more resources on exposures with higher stakes. A successful SIF prevention process incorporates efforts to control SIF exposure into the existing elements of your safety management system.
Has our SIF prevention process kept up with organizational change?
We recently worked with an organization that had initiated a robust SIF prevention process four years earlier. Today, classification data and comprehensive information is available to see the current exposure profile. However, things in the organization have changed over those years – an acquisition, policy changes and advances in other safety activities. A new data review showed that two exposure categories have emerged as more important than four years ago. Implementation tools must be revised and improved. Remember: SIF prevention processes are dynamic and need periodic reviews and process changes.
Have we restructured our incident investigation process to focus on SIF potential?
A proportionate response is a powerful element. Creating a two-tier incident investigation process shifts the investigation effort to those incidents with significant potential for harm. OSHA recordables are investigated, but those with a low potential for actual SIF outcomes are investigated locally or with a less-intensive process. All incidents classified with SIF potential are more thoroughly investigated.
One of the most important things organizations and leaders do to retain a highly engaged workforce is to show concern for their employees. And when we control SIF exposures, we show that we care.
This article represents the views of the author and should not be considered a National Safety Council endorsement.
Erika Gwilt is a vice president in DEKRA’s consulting practice. Her extensive experience in leadership development and business strategy enables her to help clients engage their workforce in improving safety outcomes. Gwilt’s expertise includes leadership coaching, sustainable safety performance, and SIF analysis and prevention.
Elizabeth Prazeres is an organizational effectiveness and change management expert at DEKRA. Her experience includes organizational change, human performance reliability and safety leadership. Prazeres has worked in various industries, including oil and gas, utilities, manufacturing, equipment rental, transportation, chemical, and energy.
Direct to your inbox: Sign up to be notified in email about new "Safety Leadership" columns.
Post a comment to this article
Safety+Health welcomes comments that promote respectful dialogue. Please stay on topic. Comments that contain personal attacks, profanity or abusive language – or those aggressively promoting products or services – will be removed. We reserve the right to determine which comments violate our comment policy. (Anonymous comments are welcome; merely skip the “name” field in the comment box. An email address is required but will not be included with your comment.)