More of OSHA’s ‘most interesting cases’
What happened – and what not to do

Page 2 of 4
CASE #1
Death related to unguarded machinery
An employee of a polypropylene product manufacturer was killed after she was pulled into a roller machine.
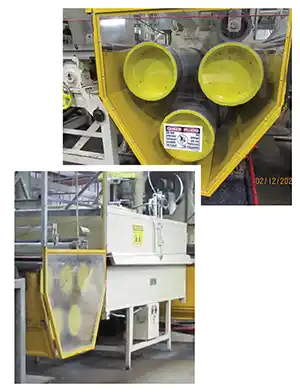
As part of the abatement process, the employer enclosed the rollers that had no guarding.
The worker was instructed to reach into the machine to cut “wraps,” which would occur when a polypropylene fiber strand being pulled through the process broke and then balled or rolled up on the roller itself. This could cause production to stop. Employees would use handheld scissors or knives to cut wraps while the machine was running.
During an inspection, OSHA observed rollers without adequate guards or guards that were left in the up position. The employer didn’t require employees to pull down the guards, when they were available, and didn’t train workers on lockout/tagout procedures.
In the three years before the inspection, the employer had 15 recordable cases involving employees working near the rollers. In six of those cases, fingers, hands or hair were caught in or between the polypropylene web and/or the rollers. The rest involved cuts that happened while employees were attempting to remove wraps from the rollers.
OSHA/legal actions: The agency cited the employer for 16 violations, including eight serious violations, with fines totaling $195,144. The employer paid $155,338 in penalties after a settlement.
The family of the victim was awarded $3 million in a wrongful death suit, and the company pleaded guilty to federal charges, resulting in an additional $410,856 in fines and restitution.
Resolution: The employer abated all hazards identified by OSHA.
That included developing long-reach tools so employees could cut wraps while staying out of the danger zone. Interlocks were installed so the machine stops if a guard is opened, moved or changed. The rollers with no guarding were enclosed to keep workers from reaching into the nip point, “except where the web had to enter and exit the rollers.” Additionally, the employer conducted lockout/tagout training for all employees.
Lessons learned:
- Don’t bypass safety for production.
- Complete a risk assessment and eliminate or mitigate identified hazards.
- Train all employees on the hazards of a process and how to prevent exposures.
- Investigate incidents and take actions to prevent a recurrence. Inaction is a willful violation.
Post a comment to this article
Safety+Health welcomes comments that promote respectful dialogue. Please stay on topic. Comments that contain personal attacks, profanity or abusive language – or those aggressively promoting products or services – will be removed. We reserve the right to determine which comments violate our comment policy. (Anonymous comments are welcome; merely skip the “name” field in the comment box. An email address is required but will not be included with your comment.)