Lockout/tagout responsibility
Who is responsible for lockout/tagout within a facility?
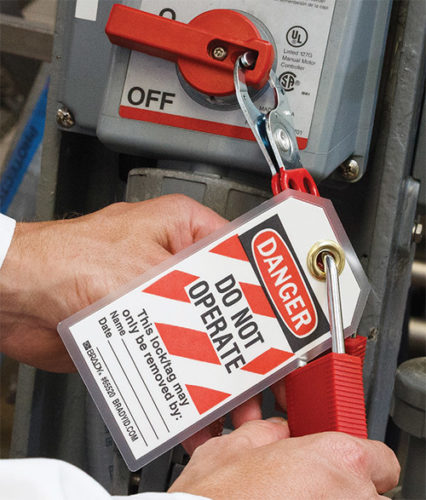
Responding is Courtney Bohman, regional product manager, Brady Corp., Milwaukee.
Effectively implementing a sustainable lockout/tagout system can be a daunting task. Navigating the regulations, having suitable devices on hand and appropriately training both authorized and affected employees can be a full-time job at most facilities. At Brady Corp., we are often asked who within a facility has ultimate responsibility for lockout. The answer to this question is simple – everybody does. The best way to ensure a consistent, well-run lockout program is to have the support and involvement of all levels of the company.
An effective lockout/tagout program begins with management buy-in. A facility’s executive team is responsible for setting the vision and implementing corporate protocols. They are also responsible for perpetuating company values around a culture of safety. This culture is the cornerstone to successful implementation. The executive team should also participate in investigations and audits, and conduct operational risk reviews. Active engagement before, during and after implementation is key.
Moving down one layer, front-line managers are responsible for a number of the tactical needs of a lockout system. They institute machine-specific procedures; conduct training and audits; keep the executive team informed on successes, concerns and issues; and drive continuous improvement on the manufacturing floor. Front-line managers serve as the conduit between the employees and the executive team, supplying both with the tools and information needed for sustainable success.
Once the processes and protocols are implemented, responsibility shifts to the employees. Authorized employees have the clearest lines of responsibility. They maintain appropriate knowledge, skills and abilities to perform lockout activities, while demonstrating a safety mindset throughout the process. They also perform their lockout duties in all instances in which maintenance is required and follow documented procedures. Finally, they assume control for the health and safety of their fellow employees.
To those who believe responsibility ends with the authorized employees: think again. Affected employees also play a key role. These individuals need to be active participants in general safety training. They need to maintain awareness of lockout procedures for all pieces of equipment in their work area and they must heed the necessary warnings illustrated through the placement of a lockout device. Without affected employee cooperation, a fully developed lockout/tagout system could fall apart.
The goal of any lockout system is to emphasize safety, maintain compliance and promote sustainability. To accomplish those three goals, it is absolutely critical that all layers of the organization take responsibility for the implementation, performance and evaluation of lockout. The most successful systems marry the skills of the full corporate hierarchy.
Editor's note: This article represents the independent views of the author and should not be construed as a National Safety Council endorsement.
Post a comment to this article
Safety+Health welcomes comments that promote respectful dialogue. Please stay on topic. Comments that contain personal attacks, profanity or abusive language – or those aggressively promoting products or services – will be removed. We reserve the right to determine which comments violate our comment policy. (Anonymous comments are welcome; merely skip the “name” field in the comment box. An email address is required but will not be included with your comment.)