2018 CEOs Who "Get It"

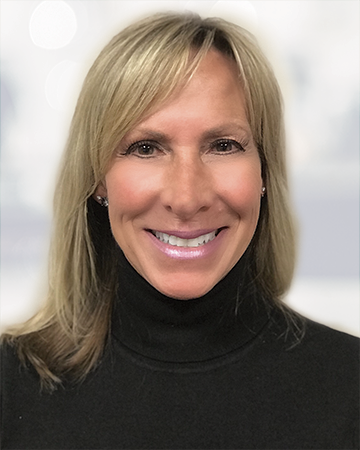
Tammie Johnson
President and CEO
CJ Drilling
Dundee, IL
CJ Drilling is a 100 percent woman-owned and operated foundation drilling contractor serving the utility, transportation, railroad and general contracting industries. The company also provides heavy-hauling; rebar cage fabrication; crane hoisting; hydro-excavation; concrete pumping and finishing; and site access, cleanup and remediation. CJ Drilling employs 115 workers.
Describe your personal journey to becoming a CEO who “gets it.” What experiences or lessons brought you to where you are now?
I set a goal to never miss out on a bid opportunity because of our past safety performance, and I can proudly say we never have. We have actually passed on some bidding opportunities because of safety concerns. More and more, we see our customers examine our past safety performance, safety programs and our regulatory compliance record before we even begin to estimate a job. This has become the “price of admission” to work for most of our customers. As the president/CEO, it is up to me to ensure we do not lower these standards. Not even for a minute.
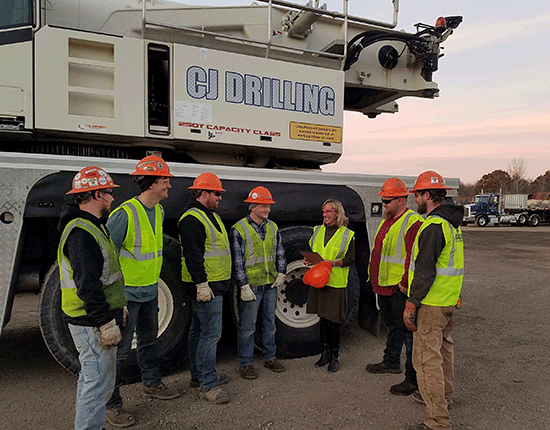
Why is safety a core value at your organization?
Nothing is more important to our overall success than our employees going home safe each and every day. I owe it to our employees to provide the resources necessary to prevent injuries and incidents. This is a commitment that I take personally and I require throughout every level of employment within the company. By sharing this value across the organization, safety does not become one person’s responsibility; rather, it is a shared responsibility across all levels of our company. This allows us to protect our employees, our customers and the public as we perform our work. In our very competitive market, our company would simply not exist if safety wasn’t a core value.
What is the biggest obstacle to safety at your organization, and how do you work to overcome it?
One of the biggest obstacles to safety at CJ Drilling is the human performance factor. All humans are fallible. There’s just no getting around it and, sometimes, despite their best intentions, they may disregard a safe work procedure in an effort to get a job done. While we admire ingenuity and reward innovation, we have to remain vigilant in communicating that all changes in the procedure must be evaluated to ensure that safety is built in. We will never eliminate people in our workforce, so it is up to us to ensure every employee fully understands their role in delivering our product safely to our customers. Our customers demand it of us, and we owe it to our employees.
How do you instill a sense of safety in employees on an ongoing basis?
The most important thing we can do as a company is to remain consistent with our safety message. Although we perform work all over the country, our safety message doesn’t change. We need to ensure our employees receive the same support for their safety on any project and working for any of our field leaders. To make sure we continuously send the same message, we have a weekly safety conference call to share the same safety message to all of our company leaders. This call is followed up with the minutes being made available to every employee. By sharing a consistent safety message and communicating our safe work expectations, we have seen a reduction in incidents in each of the past five years.
How does your organization measure safety?
We monitor and report out on several safety metrics. In no particular order, we look at incident by cost, incident type, root cause, the supervisor at the time of the incident, geographic location, weather, etc. Each of these metrics allows us to identify positive and negative trends so that we can provide the resources, be it worker oversight, training, equipment or a combination, where they are needed the most.
What are the leading indicators that show you how safe your organization is, and where do you see room for improvement?
Monitoring these metrics is an important part of how effective our safety program is, but they are all reactive – that is they only show what we’ve done. To counter that, I have instructed our safety director to take a very hands-on and proactive approach to our safe work performance. This approach is again a team approach. In addition to our weekly safety call I mentioned, our field leadership performs an audit of their jobsite a minimum of once weekly. This allows us to identify deviations from our safe work practices before an incident occurs. We also take a team approach to investigating all incidents, even if an injury does not occur. Our incident analysis team is assembled and includes myself and all senior managers, safety staff, the person(s) involved in the incident as well as field leadership. This investigative process allows several independent views on the incident and allows us to figure out what went right, what went wrong and what needs to be fixed.
We continually strive for zero incidents and have committed personnel and resources to our safety program. One area that we can improve is to ensure that every safety message we send is received and understood by every employee. With modern technology, it has become very easy to electronically send a safety communication, but we need to work harder to ensure the receiver understands the message so that the same incident doesn’t happen again.
What role does off-the-job safety play in your organization’s overall safety program?
Safety off the job is just as important to us as it is on the job. There are so many of our safe work procedures that parallel activities outside of work: texting while driving, ladder use, smoke detectors, ergonomics, fire prevention, etc. I hope that our employees utilize the same practices off the job to ensure their safe return to work – we cannot be successful without them. As a NSC First Aid, CPR and AED training center, we provide this training to all of our employees. This valuable training is available to our employees whether they experience an accident at work, at home or out in the public.
What types of off-the-job safety and health programs does your organization offer to employees?
In 2016, we built a gym and basketball court to allow our employees a place to work out. This facility is open to all employees, and they have 24-hour access to it. Throughout the year, we send out safety messages that are relevant to safety in the home, like during Fire Prevention Week, Fourth of July Summertime Safety and Winter Holiday safety tips. In coordination with our health care provider, we provide information on nicotine cessation to help our employees quit their nicotine usage. It is my goal to be a tobacco-free company by 2020.
Post a comment to this article
Safety+Health welcomes comments that promote respectful dialogue. Please stay on topic. Comments that contain personal attacks, profanity or abusive language – or those aggressively promoting products or services – will be removed. We reserve the right to determine which comments violate our comment policy. (Anonymous comments are welcome; merely skip the “name” field in the comment box. An email address is required but will not be included with your comment.)