Cleaning and housekeeping best practices
How does good housekeeping yield fewer injuries and higher profit?
Responding is Glorianna L. Corman, REM, CHMM, CSP, senior risk management consultant, KPA LLC, Lafayette, CO.
We’re all hard-pressed for time these days, which makes it hard to keep our workspaces organized and clean. A comprehensive approach to cleaning and housekeeping yields results in terms of improved safety and a healthier bottom line. But if you lack the time or resources to implement a full housekeeping program, start with a few simple best practices. Even a basic program can save your company money and reduce workplace injuries.
Step 1: Teach employees to clean up after themselves.
Make housekeeping a training priority. Recognize employees who keep their work areas clean, and encourage those who don’t to change their habits.
Step 2: Institute a schedule for routine cleaning.
Just as it is in your home, cleaning at work is an ongoing job. Create a schedule to help, employees understand that housekeeping is a routine task that’s part of the job. You may want to include safety equipment inspections in that schedule and assign someone to check your fire extinguishers, eyewash stations, tanks and other equipment.
Step 3: Properly store flammables, sharps and other hazards.
Anything that can cause illness or injury needs to be organized and put away first. If you don’t do anything else to clean, always clean up your hazards.
Step 4: Keep tools and materials organized.
Find a place for everything. One trick is to use tape on the floor to designate where things go. This makes it easier for workers to find what they’re looking for and keep areas clear.
You can see how a few basic practices will result in fewer injuries. If sharps and hazards are cleaned up, the floor is clean and supplies are tidy and stowed, the risk of injury is reduced. But how does excellent housekeeping translate into a healthier bottom line? Let us count the ways.
1. Less waste
Implementing housekeeping best practices reduces waste. Clutter and disorganization consume time and company resources without adding value. Cleanliness equals efficiency, and efficiency equals lower costs.
2. Increased employee retention
A clean and user-friendly work environment also means happier employees. An employee who takes responsibility for his or her work area tends to also take pride in it. Happier employees are more likely to stay at your company, which reduces turnover and your hiring costs.
3. Fewer repairs
When equipment goes unchecked and unmaintained, it wears out faster. By cleaning your machines and tools, you’re staying ahead of potential issues. You’re keeping minor wear and tear from developing into major problems and, ultimately, extending the working life of your equipment. This means fewer repairs and less frequent replacements.
4. Reduced fines
OSHA fines are more than $13,000 per violation, and 10 times as much for a repeated and willful violation. Considering that many injuries and OSHA violations are related to poor housekeeping, this is one risk you cannot afford to ignore.
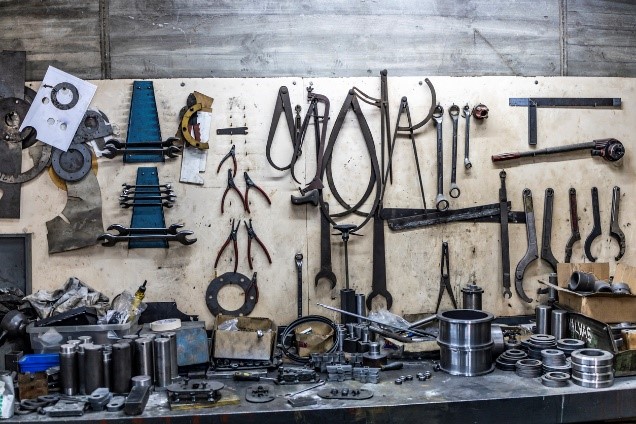
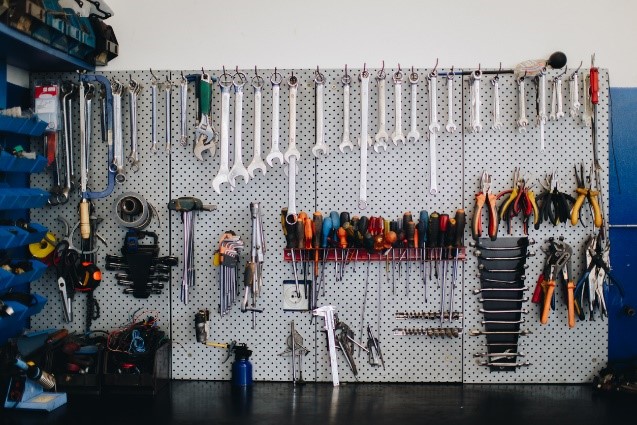
Which workspace would you rather have? It’s hard to find time to stay organized, but if you’re able to take a few small steps, you’ll save money and improve workplace safety.
Editor's note: This article represents the independent views of the author and should not be construed as a National Safety Council endorsement.
Post a comment to this article
Safety+Health welcomes comments that promote respectful dialogue. Please stay on topic. Comments that contain personal attacks, profanity or abusive language – or those aggressively promoting products or services – will be removed. We reserve the right to determine which comments violate our comment policy. (Anonymous comments are welcome; merely skip the “name” field in the comment box. An email address is required but will not be included with your comment.)