2021 CEOs Who 'Get It'

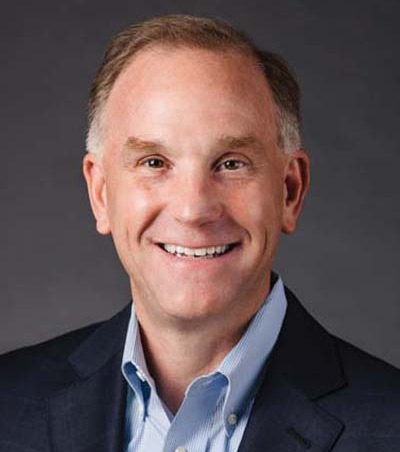
Jeff Owens
CEO
Advanced Technology Services Inc.
Peoria, IL
Advanced Technology Services Inc. is a leading industrial services provider with more than three decades of proven experience in technology-driven industrial maintenance and MRO asset management. Through a technically skilled workforce, standardized processes and Manufacturing 4.0 technologies, ATS delivers improved asset health and productivity to many leading process and discrete manufacturers.
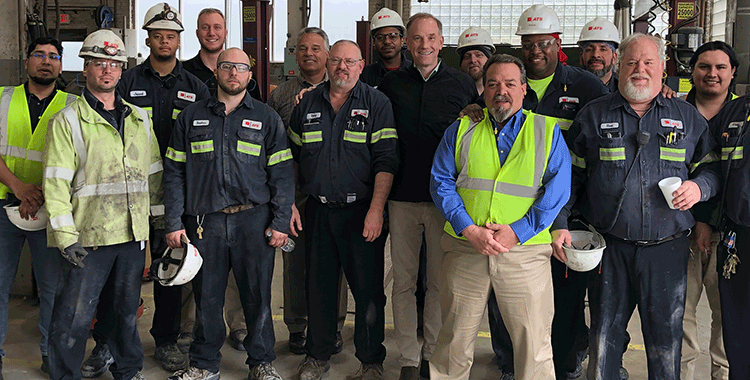
Describe your personal journey to becoming a CEO who “gets it.”
When I first joined ATS in 1988 as a sales representative, it was a small, three-year-old industrial maintenance services company just trying to survive and grow, and safety was not its primary focus. By the time I became president and chief operating officer in 2004, safety was a prominent goal but still largely compliance-focused. I committed then to raising the bar by embedding safety in the company’s overall philosophy and core culture.
One of the influences in my life that made safety so important to me was a visit to the hospital several years ago. One of our rising young maintenance technicians (now a senior leader in our company) had been injured onsite at a customer plant. A lifting strap failed and a piece of machinery fell on him, breaking his leg and sending him to the hospital. It was a first for me to visit an employee at a hospital due to an on-the-job injury.
I vividly remember walking in and feeling sick to my stomach. While being there and talking with the employee and his father, I realized I was trying to make something terrible seem OK, or at least better, but what I really needed to do was prevent anything like that from ever happening again. That day was a turning point for me. As I left the hospital, I made a personal commitment to take action. I knew that safety excellence was ultimately my responsibility and I owed it to every employee and their families to do whatever necessary to implement a culture that put us on a path to zero incidents.
The journey to our current Live Safety/Beyond Zero culture reflects our dedication to continuous improvement. The first major milestone was establishing Live Safety as ATS’s leading cultural commitment in 2006. Live Safety encourages all employees to make safety a way of life – in and out of the workplace – instead of only focusing on zero injuries and OSHA compliance.
To bolster our zero incidents objective and reward sustained safety performance, the President’s Award for Safety Excellence was launched in 2008. It is presented annually to ATS sites that achieve 12 consecutive months of meeting a defined criterion.
In 2014, I set a new requirement that all area business managers, site managers and site supervisors would obtain the Board of Certified Safety Professionals Safety Trained Supervisor certification within 12 months. We currently have over 160 employees holding STS certification and ATS is a BCSP Diamond Sponsor.
That same year, our Safety Dashboard was launched. The dashboard represents our recipe for an incident-free environment, and I continually challenge our leadership team and the environmental, health and safety team to refine and improve it. The President’s Award for Safety Excellence was connected to the dashboard in 2016.
By 2018, I believed the time was right to take our Live Safety culture to the next level: encompassing the overall well-being of every employee, in and outside of work. As a result, Beyond Zero replaced Incident Free as a subtext to our Live Safety brand.
Last year marked the introduction of the Beyond Zero Challenge. It is a personal award for employees completing certain safety and well-being activities over the course of a year, such as identifying hazards, performing inspections or improving personal well-being in some manner.
There are countless additional ways we have worked to ingrain the Live Safety/Beyond Zero culture. It is one of the four key management systems in our operating system (safety, people, process and technology), the first topic at executive meetings, discussed repeatedly on the job, trained and reinforced routinely, visible on company graphics, and so much more. I have found it personally rewarding to see the positive impact our safety initiatives have had on our team over the years – both on the job and in their personal lives.
What is the biggest obstacle to safety at your organization, and how do you work to overcome it?
Ensuring the safety of thousands of employees serving hundreds of customer manufacturing facilities across the United States, the United Kingdom and Mexico is no small feat. Varying job risks, non-routine tasks, diverse plant environments and varying customer expectations all pose a challenge.
We have several strategies to address these obstacles:
- Screening potential new employees and leaders with challenging safety-related questions in the interview process
- Training site leaders on their role in creating an environment where employees are motivated to Live Safety 24/7
- Conducting pulse surveys two to four times a year to get the “voice of the technician”
- Maintaining strong safety management systems that are focused on continuous improvement and flexible to encourage employee engagement and ownership
- Reducing risk to ATS and customer employees by improving their “eyes for safety” through education as well as hazard reporting and management
Why is safety a core value at your organization?
Simply put, we care about and value our employees. Many of our employees are maintenance technicians, and due to the nature of their job, they will perform potentially hazardous tasks. Our programs are intended to provide our technicians the education and resources they need to make the right decisions on how to safely execute each task.
Furthermore, we strongly believe that our success begins with having a strong safety culture. Live Safety is the first of our four cultural pillars because it is fundamental to success:
Live Safety: Safety excellence and personal well-being are foundational. Employees need to think it, feel it and live it every day.
Value Employees: Without knowing that ATS cares about their safety, employees would not feel valued.
Engage Customers: Without valued employees, customers would not be engaged.
Drive Results: Without engaged customers, ATS would not get results.
How do you instill a sense of safety in employees on an ongoing basis?
I made it my personal mission to ensure ATS has the right systems, processes, investments and people in place to help all employees move beyond the Zero Incident objective and to a holistic Live Safety/Beyond Zero culture.
All employees receive an aggressive, 90-day safety orientation with topics ranging from compliance-based training to Live Safety, job safety analysis, safety conversations and the Beyond Zero core elements. Beyond Zero tips and weekly toolbox talks are designed to educate and engage the team in conversations about the subject. Each monthly Eyes for Safety publication focuses on a specific physical hazard to help improve hazard recognition and reporting.
Site employees are awarded and recognized with the President’s Award for Safety Excellence when their 12-month score on the Safety Dashboard is 100% or greater. Individual employees are recognized though our Beyond Zero Challenge with our GEAR (Gratitude & Encouragement through Acknowledgement & Recognition) program or with a culture coin when they demonstrate the ATS Live Safety principles.
I also believe a strong safety culture starts with strong leadership. For example, all site leaders are provided a full day of training on creating a culture that motivates employees to Live Safety 24/7. Also, when executives and area leaders visit a site, they are tasked with completing a Leadership Site Visit Observation, which requires them to engage with the technicians and evaluate their perceptions of the key safety activities at the site. Afterward, feedback and coaching are provided.
How does your organization measure safety? What are the leading indicators that show you how safe your organization is, and where do you see room for improvement?
The Safety Dashboard reflects leading indicators (proactive activity) rather than lagging indicators such as accidents. Site managers are responsible for their index scores on the dashboard. It currently measures safety training, the percentage of the workforce observed through leadership safety observations, corrective action completion, safety inspection completion, self-assessment completion, Plan-for-Zero status and toolbox talk delivery. Our biggest challenge is keeping the actions that are measured transformational and not transactional (checking a box).
Our focus on leading indicators is helping our lagging indicator performance. We are proud that ATS has achieved world-class safety performance as measured by the OSHA recordable incident rate and OSHA lost-time rate. In fact, two impressive new milestones were reached in 2020:
- 89 days/>1M hours without a recordable incident
- 144 days/>2M hours without a lost time incident
What role does off-the-job safety play in your organization’s overall safety program? What types of off-the-job safety and health programs does your organization offer to employees?
Our Live Safety 24/7 culture encourages all employees to make safety a way of life, in and out of the workplace. Because safety excellence and personal well-being are foundational, we want our employees to think it, feel it and live it every day.
The success of our program relies on safety being a value or “state of being” (both conscious and subconscious), instead of just a priority – not only for our employees but also for family, friends, co-workers and customer employees. An ideal ATS employee will be able to confirm the following statements without hesitation:
- “I am open to initiating safety conversations with others.”
- “I am passionate about making a difference relative to safety in our company.”
- “I don’t care what others think. If I feel it is the right thing to do from a safety standpoint, I’ll fight for it.”
What have you done to support employee mental health and well-being within your organization?
Because personal distractions are just as much a safety risk as technical errors, we stopped using the term “incident-free” and started using Beyond Zero to create a culture of well-being throughout ATS. Beyond Zero encourages employees to continually improve their well-being for themselves, family and friends, and includes five interconnected core elements: Live Safety 24/7, physical well-being, emotional well-being, social well-being and financial well-being.
The Beyond Zero Challenge is a platform designed to educate and motivate employees on each of the five core elements, with resources and tools for the employees and their families.
Examples include employee testimonials, online training, toolbox talks, daily Beyond Zero tips, and holiday-centered “stand-downs” that focus on internal and external factors that could impact an employee’s emotional well-being and lead to a “mind not on task” incident.
In 2020, a multifunctional team was chartered to review the metrics related to the employee assistance program and provide specific actions to highlight the benefit for the employees and their families.
One thing I can promise is that ATS’s commitment to a strong safety culture and our employees’ well-being will never waver, and our journey for continuous improvement will never end.
Post a comment to this article
Safety+Health welcomes comments that promote respectful dialogue. Please stay on topic. Comments that contain personal attacks, profanity or abusive language – or those aggressively promoting products or services – will be removed. We reserve the right to determine which comments violate our comment policy. (Anonymous comments are welcome; merely skip the “name” field in the comment box. An email address is required but will not be included with your comment.)