Safety Leadership: The economy is picking up – make sure safety doesn’t let down
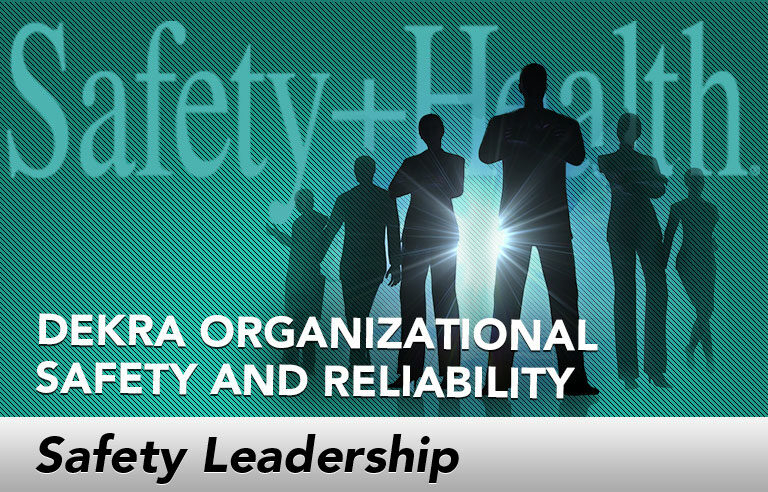
Editor’s Note: Achieving and sustaining an injury-free workplace demands strong leadership. In this monthly column, experts from global consulting firm DEKRA Insight share their point of view on what leaders need to know to guide their organizations to safety excellence.
Business is looking bullish. Fed policymakers forecast a 3.6 percent unemployment rate by the end of the year, with 2019 and 2020 expected to see even lower levels. What’s more, in the first quarter of 2018 alone, businesses ramped up capital expenditures at a record pace, according to a recent Wall Street Journal report.
These are bullish statistics indeed, and indicative of a strong economy with strong industrial production. But safety and operations leaders know that this investment and growth comes with a set of unique risks and exposures.
Growth means new employees who are unfamiliar with existing hazards and safe work procedures, making them (and those they work with) more susceptible to errors that lead to mishaps or injuries. According to data gathered by the Bureau of Labor Statistics, employees with less than one year of service with their employer made up 32 percent of lost-time injuries in 2016 (the most recent year data of this nature is available). That’s a total of 283,630 injuries to new employees in a single year.
Extended production also carries risks, as companies struggle to meet increased demands. Ongoing overtime and the resulting human and equipment fatigue can result in exposures often overlooked by organizational leaders. To keep up with demands, companies may be forced to ask more of employees, extending overtime hours and having workers take on projects without proper training. As a result, there frequently aren’t enough qualified workers at the site to prevent overtime levels from increasing. In turn, the more overtime hours worked by the current labor pool, the higher the sickness absences, staff turnover and injury potential. BLS data for 2016 indicates that 10 percent of lost-time injuries (87,640) occurred after an employee had worked longer than an eight-hour shift.
Newly purchased equipment and facility construction also can contribute to risk if safety procedures aren’t updated or construction is started without applying Prevention through Design safety principles. Without preventive safety procedures, employees have no choice but to use their own risk acceptance and risk tolerance calculus when working around new exposures, leaving them at risk for injury.
During this expanding economy, business leaders should ask themselves if they’re confident that they’re proactively controlling, reducing or eliminating exposures to ensure every employee or contractor can work safely.
For decades, we’ve seen companies ride the safety roller coaster. When incidents increase, the company reacts with a flurry of safety-related activities. This is followed by a period of “safety,” with decreased incidents and a sense of control before overconfidence sets in and old habits return. Unfortunately, we can never be effective in the long term while relying predominately on a lagging indicator such as incidents.
A safe work environment is built through an intentional, ongoing and strategic focus on exposure reduction, rigorously executed over time through all business cycles – both upturns and downtimes. Exposure reduction is best accomplished through a broad, systemic safety approach that improves:
- Culture
- Exposure control systems
- Governance
- Leadership
- Organizational reliability
- Performance management systems
- Working interface (exposure to hazards)
We’ve all heard the cliché in business that “a rising tide lifts all boats.” Although an expanding economy certainly creates many positive outcomes in business, it’s our responsibility as leaders to ensure safety systems are just as buoyant as our bottom lines and shareholder returns.
This article represents the views of the authors and should not be construed as a National Safety Council endorsement.
Craig Hathaway is the senior vice president of marketing and business development at DEKRA Insight (dekra-insight.com). He is an executive coach and consultant who partners with company leaders to design and execute safety performance with a focus on culture-change initiatives to improve safety performance in client organizations.
Direct to your inbox: Sign up to be notified in email about new "Safety Leadership" columns.
Post a comment to this article
Safety+Health welcomes comments that promote respectful dialogue. Please stay on topic. Comments that contain personal attacks, profanity or abusive language – or those aggressively promoting products or services – will be removed. We reserve the right to determine which comments violate our comment policy. (Anonymous comments are welcome; merely skip the “name” field in the comment box. An email address is required but will not be included with your comment.)