3D printing and worker safety
Exploring the hazards of this emerging technology
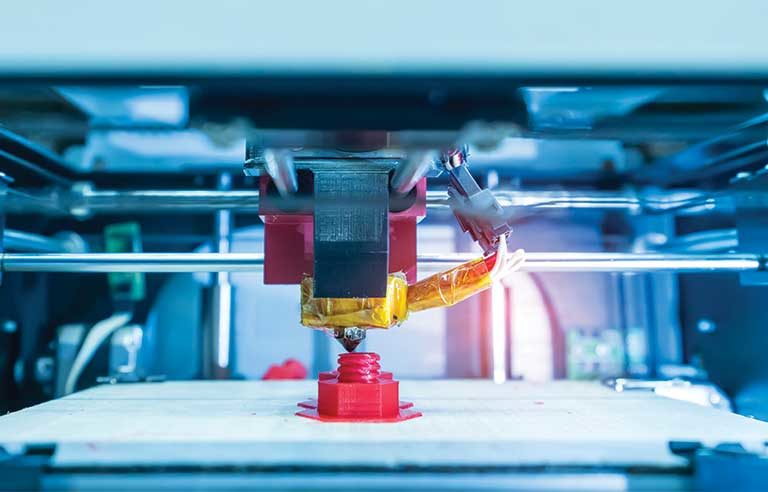
Take a digital design and layers of plastic filament or metal powder, load them into a printer and await the creation of an object that could range in weight from a few ounces to a quarter ton.
This is 3D printing, an additive manufacturing technology that has experienced widespread growth across numerous industries in recent years.
“It is almost a ubiquitous technology that’s being used in many, many sectors, from heavy manufacturing all the way down to small, private, home-based or microfactory industries,” said Chuck Geraci, associate director for emerging technologies at NIOSH.
However, as NIOSH notes in an August post on its Science Blog, “3D printing is still a relatively new technology, and there are many gaps in the information available about health and safety implications.”
Emissions considerations
Potential hazards of 3D printing involve worker exposure to emissions from heated filaments, polymers or powders. Experts say the risk depends on the engineering requirements of the object being printed, the material from which it’s produced and the printing method itself. Occupational exposure limits for 3D printer emissions have yet to be established.
In addition, Geraci points out that effective methods for controlling exposure will change “if you move from one type of 3D printing tool or device to another.”
Some desktop 3D printers emit ultrafine particles and mixtures that may be carcinogenic or cause other adverse health effects, a 2013 study from the Illinois Institute of Technology found. Styrene, a particle that comes from acrylonitrile butadiene styrene, or ABS, filament, is considered a possible carcinogen by the International Agency for Research on Cancer. And the Centers for Disease Control and Prevention has found that caprolactam – which originates from materials printed with laybrick, laywood, nylon and plasticized copolyamide thermoplastic elastomer, or TPE, filaments, according to the IIT study – is a potential irritant to eyes and the respiratory tract.
“Just switching to a low-emitting filament is certainly one of the easiest things you could do,” said Brent Stephens, study lead author and chair of IIT’s department of civil, architectural and environmental engineering. “One issue, however, is that for expert users, there are some filaments [that] have properties that users really want that may not be low-emitting.”
Still, as part of a 2018 collaboration with MakerBot, a Brooklyn, NY-based manufacturer of 3D printers, NIOSH researchers found that the particle emission levels of some filaments were lower than those depicted by IIT and similar studies. The agency recommended additional research to identify low-emitting filaments.
In Stephens’ view, more data could pave the way to a more advanced – and environmentally safe – process for selecting filaments.
“You have a chance, I think, in the near future … where maybe manufacturers of filaments and/or printers, retailers or whatever it is decide to start sending their products … to be evaluated for gas and particle emissions,” he said. “And you could imagine that you go to the online shop to get filaments and you have a label informing consumers on emissions under typical conditions.
“The problem is, [printers and filaments] just haven’t been tested very widely yet, so there’s no central database or anything like that.”
Engineering controls limit hazards
Selecting a filament is one example of an administrative control in NIOSH’s interpretation of the Hierarchy of Controls, a means of identifying and mitigating hazards before work begins. One rung above administrative controls are engineering controls, which are considered more effective. Engineering controls for 3D printing include:
Printer design. “The design characteristics of the 3D printer itself might influence emissions,” NIOSH concluded in a 2016 study, noting that different printer covers might limit the volume of air that contains emitted particles. Presenting a hypothetical scenario of a printer jam, the researchers suggest that users’ likely initial reaction – opening the cover to investigate the problem – would increase worker exposure to emissions. As an alternative, NIOSH recommended designing the printer to enact an automated shutoff of the nozzle heater should a jam occur.
Zac DiVencenzo is chief operations officer at JuggerBot 3D LLC, a 3D printer manufacturer in Youngstown, OH. “Designing with the intent to reduce the amount of access points that could harm an operator is always the first mindset,” DiVencenzo said. He recommends building printers that have limited open slots in which a user could place his or her hands, reducing the risk of contact with sharp edges or moving parts that could cause cuts or contusions. Using locks also can keep unauthorized workers from accessing certain printer functions.
Ventilation. Ventilation is an important step in helping to mitigate printer emissions.
Again, the printing method dictates the approach. A single-use local exhaust ventilation system or snorkel fume extractors would be more appropriate in smaller operations with only one printer. For setups with multiple printers, consider placing the printers on enclosed ventilated racks that filter emissions outdoors.
Another option involves using a room air cleaner that features high-efficiency particulate air, or HEPA, filtration to exhaust printer air.
“If you can operate in a sealed enclosure with a good filter for gases and particles, that can help,” Stephens said. “If you can operate with really targeted spot ventilation – just like you would a saw or a laser cutter or other tool like that – that’s probably the best thing you could do.”
Equipping workers with personal protective equipment such as a respirator is a final resort if other emission control methods prove insufficient.
Other controls
Geraci said other NIOSH researchers have visited workplaces that prohibit unauthorized employees from entering the 3D printing rooms where large-scale printers or large numbers of printers are in use, unless maintenance or other action is needed.
In any event, experts recommend allowing enough time for the printer extruder to cool before retrieving the printed product after operation, which limits potential exposure to hot surfaces. It’s also important to monitor the condition of power cords and be mindful of the risks of electrical shock.
DiVencenzo advises placing stickers in optimal positions on the printer or printing room door to signify whether an area is too hot to touch or otherwise hazardous.
“You have to do a good job using visual aids,” DiVencenzo said. “You can’t just put three stickers and hide them in a corner. They have to be practical. Someone is opening the door – where do their eyes first go? Putting visual aids in locations people can witness and see that is practical. That’s pretty big.”
Industrial-sized printers
Many industrial-sized printers feature a degree of built-in self-containment. Ample, isolated space is vital to allow laser or electron beams to fuse metal powder – which typically is more expensive than filaments or polymers – to print larger-scale products.
“It being enclosed is an extra level of safety,” DiVencenzo said. “By nature, any closed machine already starts off the right way.”
Even so, loose powder or dust may be a concern when removing an object from the printer or as printing jobs accumulate. As with filaments, powders are complex. Some are hazardous, while others are not, depending on the composition.
The Department of Energy’s Office of Scientific and Technical Information cautions that various dust hazards may be present in industrial-sized 3D printers, including skin, eye and respiratory irritants; chemical hazards from toxic metals or reactive metal pairs; and fires or dust deflagrations from combustible dust.
OSHA tips on combustible dust safety include:
- Installing a hazardous dust control program that includes dust inspection, testing and housekeeping. Ensure employees are trained on combustible dust hazards.
- Outfitting facilities with proper dust collection systems and filters.
- Regularly inspecting open and hidden areas for dust residue. Should ignition sources exist, use cleaning methods that don’t generate dust clouds.
- Using vacuum cleaners approved for dust collection.
Future developments
In 2016, the International Organization for Standardization and ASTM International began developing voluntary safety standards for additive manufacturing, including those covering general principles, design guidelines and terminology.
Because research into the technology remains ongoing, new information can always shift the dialogue, experts say.
Meanwhile, Geraci said NIOSH researchers have noted an increasing prevalence of employers who recognize that they can’t simply buy a printer, put it in place, plug it in and consider the operation ready. Training employees, performing hazard assessments and assessing printer space management are critical to creating a safe and sustainable 3D printing environment in the workplace.
Although he said he doesn’t envision future federal regulations specific to 3D printing, Geraci highlighted the continuing work of NIOSH and various other standards-setting organizations aimed at developing guidance.
“We’re not seeing anything that is so exotic or so out of the ordinary that we would have to tell people you really need to reconsider this technology,” Geraci said. “What we’re seeing is that any of the potential hazards and emissions – especially the chemical or the particulate emissions – are manageable. They are controllable. And we’ll put out as much good information as we can and guidance that we can to help you achieve that.”
Post a comment to this article
Safety+Health welcomes comments that promote respectful dialogue. Please stay on topic. Comments that contain personal attacks, profanity or abusive language – or those aggressively promoting products or services – will be removed. We reserve the right to determine which comments violate our comment policy. (Anonymous comments are welcome; merely skip the “name” field in the comment box. An email address is required but will not be included with your comment.)