Speaker Spotlight: Measuring safety excellence – a culture maturity model

EDITOR’S NOTE: Every year, the National Safety Council Congress & Expo features some of the top thought-leaders and motivators in the occupational safety and health community. Safety+Health has invited the most highly rated presenters to contribute to this monthly column. For more on this year’s event, visit congress.nsc.org.
It’s been my honor to present at the National Safety Council Congress & Expo for many years now. Last year, as I considered what my clients requested most often, I chose to speak about safety culture.
It seemed a lot of folks were getting clearer pictures of what their culture was and what they wanted it to be, but none of them had a strategic plan for how to make the transition. Although they knew the general direction they wanted to go, they had no road map to guide them.
Many referred to the DuPont Bradley Curve, as though seeing the three-step transition would somehow magically make it happen. Although this model was extracted by many to form generic steps, I’ve found that strategies always need to be customized to each organization. The goal is to provide a guideline for what must be addressed in the organization to impact the desired culture transition. Although each plan should be individualized, this model is a checklist to ensure you formulate a complete approach.
Each element of safety excellence impacts and influences the safety culture. This means that if the influencers don’t change, neither will the culture. Each element must evolve through the stages from left to right. If any of the elements don’t progress at a similar rate as the others, the process will stall, or at least be suboptimized. If strategy, leadership and engagement don’t evolve, neither will culture. If metrics aren’t developed to measure the progression, it’ll be impossible to manage the change.
Once an organization has the big picture of what culture improvement entails, then the implementation of the steps can be planned and executed. Failure to fully appreciate and address these necessary steps usually results in wishful thinking rather than meaningful progress. Having a visual representation of the necessary steps also facilitates leaders to grasp what’s necessary and mentally map it toward completion.
Begin at the left of the model (below) and trace each element in the first column from left to right. This is what must happen to achieve safety excellence while shaping a safety culture that will sustain the improvements.
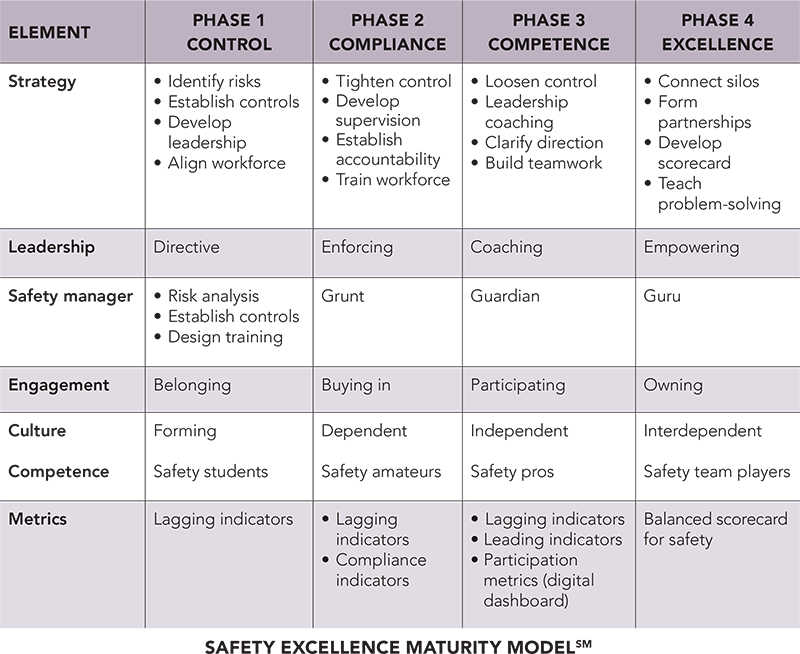
This article represents the views of the author and should not be construed as a National Safety Council endorsement.
Terry L. Mathis, founder and CEO of ProAct Safety, has served as a consultant and advisor for top organizations worldwide. A respected strategist and thought-leader in the industry, Mathis has authored five books, numerous articles and blogs, and is known for his dynamic and engaging presentations.
Direct to your inbox: Sign up to be notified in email about new Speaker Spotlight columns.
Post a comment to this article
Safety+Health welcomes comments that promote respectful dialogue. Please stay on topic. Comments that contain personal attacks, profanity or abusive language – or those aggressively promoting products or services – will be removed. We reserve the right to determine which comments violate our comment policy. (Anonymous comments are welcome; merely skip the “name” field in the comment box. An email address is required but will not be included with your comment.)