The 2022 CEOs Who 'Get It'

David B. Burritt
President and CEO
U.S. Steel Corp.
Pittsburgh, PA
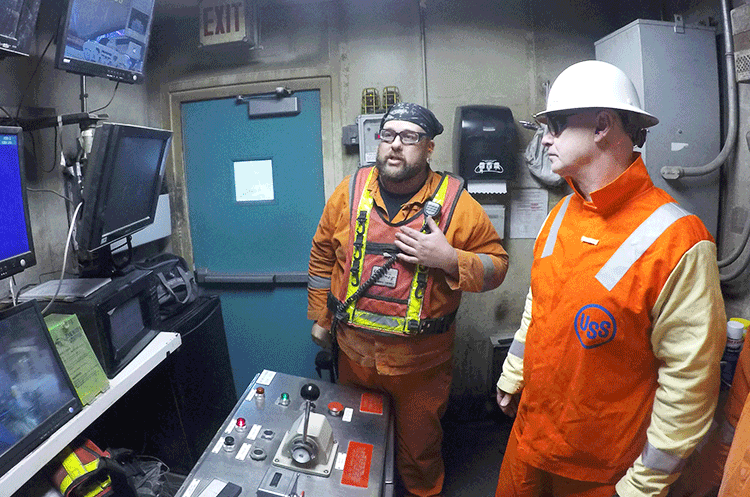
Founded in 1901, U.S. Steel Corp. is a leading steel producer. With an unwavering focus on safety, the company’s customer-centric “Best for All” strategy is advancing a more secure, sustainable future for U.S. Steel and its stakeholders. With a renewed emphasis on innovation, U.S. Steel and its more than 24,000 employees serve the automotive, construction, appliance, energy, containers and packaging industries with high value-added steel products. The company also maintains competitively advantaged iron ore production and has an annual raw steelmaking capability of 26.2 million net tons. Headquartered in Pittsburgh, U.S. Steel has world-class operations across the United States and in central Europe.
Describe your personal journey to becoming a CEO who “gets it.”
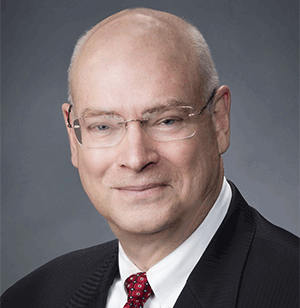
There are three important lessons I’ve learned about safety during my career. First, leaders who truly care about the employees they lead put employees’ safety first, always. That applies to all leaders, from the front lines to the C-suite and everywhere in between. Second, I’ve found that companies that can’t get safety right often get other important things wrong, too. When I was looking to join U.S. Steel in 2013, one of the most attractive things about the company was its long-held, clearly stated commitment to workplace safety. That told me that this was a company committed to doing the right things the right way. Lastly, I’m a firm believer in holding people accountable for their performance. At U.S. Steel, the safety organization reports directly to me. That’s because I want to show our employees around the world how much I care about their safety by being the executive directly accountable for it.
What is the biggest obstacle to safety at your organization, and how do you work to overcome it?
The most obvious obstacle to safety for the steel industry is that the vast majority of our employees work in high-hazard environments every day. For many years, U.S. Steel has been leveraging data and technology to drive the safety performance improvements we need to reach our goal of zero incidents and injuries. Increasing use of data has also helped us avoid another common obstacle: complacency. We’ve created a culture that empowers our leaders to use data to watch for plateaus and set new goals that will keep their employees engaged and striving for safety excellence.
Why is safety a core value at your organization?
At U.S. Steel, we believe our longevity is tied to core values built into our corporate DNA by our founding fathers back in 1901. Those core values are known today as our S.T.E.E.L. Principles. It’s no coincidence our first S.T.E.E.L. Principle – the “S” – stands for “safety first,” because safety is truly foundational to everything we do. Our “safety first” culture is one of the things that has always set U.S. Steel apart from our competitors, because “safety first” is more than a tagline for us. We coined that phrase around 1908, and we feel an intense responsibility to be a true leader on workplace safety because we believe every employee deserves to return home safely at the end of every day.
How do you instill a sense of safety in employees on an ongoing basis?
We believe our very literal approach to the expression “safety first” helps our employees understand its place within our culture. Safety is the first thing we talk about in every meeting or team huddle – from the shop floor to our board of directors meetings. During their orientation process, new employees in our plants are given cards with my signature that empower them to put safety first and stop work at any time if they deem something to be unsafe. We also work cooperatively and in highly visible ways with the unions who represent the majority of our employees because we all agree the safety of U.S. Steel employees is our top priority.
How does your organization measure safety?
U.S. Steel develops and implements safety performance indicators within each organization to ensure effective buy-in and impact for their specific issues and culture. Each operating facility has the responsibility to establish, implement, continuously evaluate the effectiveness of, and modify SPI plans as necessary. The plans must be submitted to corporate leadership for review prior to final implementation. Some of the most common SPIs are related to safety management system, hazard identification and risk assessment, employee engagement, and fatality prevention auditing. Providing this flexibility has proven to be effective because it allows the site to customize their leading indicator plan to address any gaps within the safety process or safety performance at their facility. Each SPI has targets developed for each management employee, which feed the department and overall facility targets, and performance is monitored at multiple levels throughout the organization on a regular basis.
What role does off-the-job safety play in your organization’s overall safety program?
U.S. Steel has long stressed the idea that we want our employees to be safe at work, at home and everywhere in between. We look for opportunities to provide examples of work-related safe job procedures that can be applied to common tasks performed at home by employees and their family members. We frequently reference and recommend third-party resources, such as the National Safety Council’s website and our employee assistance program, to employees in our safety-related communications. We also amplify stories our employees share with us of how they prevented serious incidents away from work thanks to safe job procedures they learned while on the job.
What have you done to support employee mental health and well-being within your organization?
In recent years, U.S. Steel recognized a need to expand how we think about safety in our workplaces. When people sense emotional threats or suffer psychological stress on or off the job, it can become a distraction at work, and distractions at work for one person can create physical safety risks for every person. Our new 360 Safety initiative aims to take a more holistic approach, focusing on the physical and psychological well-being of our employees. Our goal: create a real culture of caring at every U.S. Steel facility in which everyone feels safe, respected and confident enough to be themselves so they can deliver their best work and help themselves and our company excel. We are approaching 360 Safety from all angles – from training and regular engagement with our employees to partnerships with thought leaders and organizations such as NSC.
Post a comment to this article
Safety+Health welcomes comments that promote respectful dialogue. Please stay on topic. Comments that contain personal attacks, profanity or abusive language – or those aggressively promoting products or services – will be removed. We reserve the right to determine which comments violate our comment policy. (Anonymous comments are welcome; merely skip the “name” field in the comment box. An email address is required but will not be included with your comment.)