Ready for a safety walkaround?
We’ve got tips

The prevention side of incidents.
That’s how Tarah Kile, director of the Consultation, Education and Training Division at Michigan OSHA, describes safety walkarounds.
“Those opportunities to walk your shop, walk your floor or walk your jobsite are invaluable,” Kile said. “Any organization that doesn’t want to have an incident, wants to lower their incident rates or keep their employees safe really should participate.”
Safety professionals, management and workers from any area of an organization can take part in walkarounds, which are aimed at identifying and resolving hazards. Even in industries that have specific requirements for the timing and scope of certain inspections (construction and mining are two), conducting regular safety walkarounds can bring big benefits.
Tarah Kile, director of the Consultation, Education and Training Division at Michigan OSHA, talks about walkarounds on the June 2023 episode of Safety+Health's “On the Safe Side” podcast.
“To me, it’s one way of confirming and verifying all the training that we do, all the awareness that we do, all the communication that we do throughout the organization is actually being applied,” said David Consider, senior safety consultant at the National Safety Council.
Here are five tips for making your safety walkarounds effective.
Bring a group
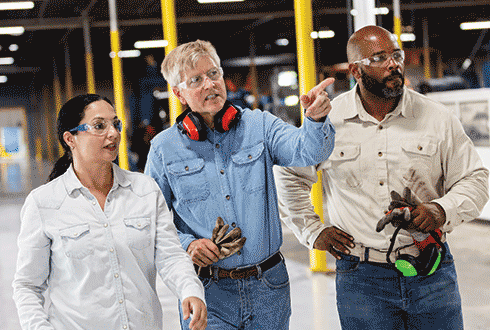
Safety doesn’t fall only on safety pros, so get others involved in the walkaround process. That could be a small group of three to four people or a larger group of eight to 10.
“At a minimum, I’m taking representatives from management and I’m taking representatives from the worker side of the house,” OSHA Region 3 Assistant Administrator Nicholas DeJesse said. “Management, obviously, because they oversee the process. Workers because they are intimately involved in every aspect of the work when it comes to the process.
“A worker will know if a process or machine is running properly. They will know when it’s running improperly, as well.”
Participation by representatives from different parts of the organization can add knowledge and varying perspectives to the walkaround process.
“Grab a janitor. Grab an accountant,” Kile said. “Somebody with a fresh set of eyes that can ask questions you don’t think to ask is really important.”
However, she cautions against making safety walkaround teams too big. “You don’t want to overwhelm the workers.”
Reward the good
Consider has an unwritten “2-to-1” rule, which involves pointing out to workers two good things for every safety hazard he discovers. Some safety pros extend it to 5-to-1, he noted.
“It’s so easy to find the things we’re doing wrong,” he said. “But what we struggle with sometimes is finding the good and recognizing the good.”
If he spots a worker not wearing safety glasses, for example, Consider’s approach would be as follows: “I’ll tell them, ‘Hey, great work area. It’s nice and clean. It’s organized. You’ve got a cord in the back that’s been identified. You’ve got some cones back there. Nice job. But, I need you to put those safety glasses on.’”
Rewarding correct behaviors, Consider added, takes away uneasiness that workers may have when the next safety walkaround takes place.
Document your findings
This can be as simple as taking handwritten notes and documenting hazards with photos, or even using an inspection app.
“If we can be more efficient and tap into technology, absolutely,” Consider said.
Kile pointed out that workers in an organization that’s new to safety walkarounds could be taken aback by a camera or a clipboard. “If you’re new to this and your culture isn’t used to it, I would say walk out with a smile and your PPE and take your notes afterward.”
The safety pro should then collect group members’ notes and photos after the walkaround and compile them in a report that begins with an executive summary. Consider suggested starting the follow-up report with positive observations before noting identified hazards/takeaways that need attention. Once the report is complete, distribute it to key members of the organization and use it as a template for future reports.
Documentation also applies to safety pros. DeJesse said that should include updates on what actions were taken. For an unguarded part on a machine, for example, that could involve communicating with employees to stay clear of the part, posting warning signs or stanchions to keep workers away until a new piece of Plexiglas is delivered, and then installing the guard.
“You don’t want to work in a factory full of nothing but workarounds,” DeJesse said. “And you never want to find 10 things, then a month later find the same 10 still not corrected.”
Prioritize fixes
Now that you’ve identified safety issues, which should be corrected first?
Experts say start with the hazards that cause immediate concern.
“If it’s immediately dangerous, we get people out of that situation,” Kile said. “There’s no question about that.”
Resources from OSHA’s Safe + Sound program include a safety walkaround fact sheet that features a hazard prioritization matrix.
It uses five levels of “likelihood of occurrence or exposure” (frequent, probable, occasional, remote and improbable), along with four categories of “severity of injury or illness consequence” (negligible, marginal, critical and catastrophic).
By using the matrix, safety pros can determine which hazards should be prioritized. (Find the matrix and more at osha.gov.)
“Anything that you find that can be fixed right away, should be,” Kile said.
Follow up, then do it again
So, let’s say your safety walkaround group has identified 10 hazards that need attention. Now what?
“I like ensuring we have a robust, quality follow-up system in place,” Consider said.
A week after the walkaround, Consider suggests going out and checking to see if a hazard has been resolved and if the solution is working. Check back again in a month, and again in three months. “Now we’re letting folks know we care about them, that we’re interested, and it’s not a one-and-done,” he said.
Fixing a guard on one machine and following up can create a template should another machine need attention. “It brings about best practices,” Consider said.
Post a comment to this article
Safety+Health welcomes comments that promote respectful dialogue. Please stay on topic. Comments that contain personal attacks, profanity or abusive language – or those aggressively promoting products or services – will be removed. We reserve the right to determine which comments violate our comment policy. (Anonymous comments are welcome; merely skip the “name” field in the comment box. An email address is required but will not be included with your comment.)