OSHA’s Top 10 most cited violations for 2019
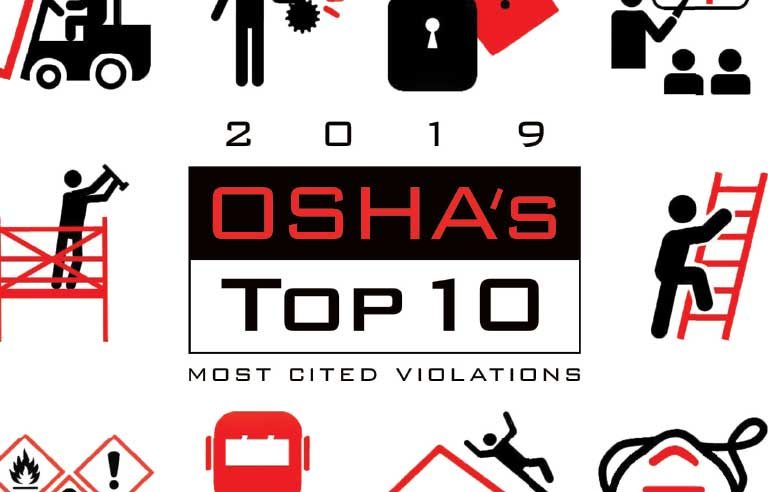
Q & A with OSHA's Patrick Kapust
Preliminary data for OSHA’s Top 10 most cited violations for fiscal year 2019 was announced Sept. 10 at the National Safety Council 2019 Congress & Expo in San Diego. Later that day, Patrick Kapust, deputy director of OSHA’s Directorate of Enforcement Programs, sat down with Safety+Health Associate Editor Kevin Druley to discuss the list, as well as strategies the occupational safety community can use to help correct hazards in their workplaces.
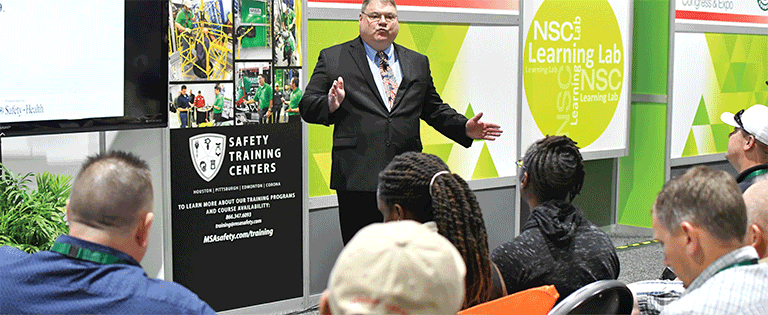
Safety+Health: Why do you think the Top 10 generally stays the same year after year?
Patrick Kapust: The Top 10 generally stays the same because employers are not aggressively targeting these hazards at their worksites. OSHA has free, readily available resources to train and educate workers to eliminate these hazards. For example, falls remain the top cited hazard for a good reason: Falls can and do result in significant injuries and deaths. But they are easily preventable.
S+H: The fall protection standard continues to top the list. What is it about the standard that yields so many violations?
Kapust: According to the Bureau of Labor Statistics, falls from elevations is the No. 1 cause of fatal injuries for construction workers. Falls are one of the “Focus Four” hazards in the construction industry. The others are caught in between, struck by and electrocution. OSHA is vigilant about identifying these hazards and getting them corrected to save lives. Employers need to be vigilant too, though. Ensuring a robust safety management system is in place will help mitigate these hazards before they become incidents, and this should be a priority for the employer. Worker participation and management commitment to a safety program are key to the success of that program.
S+H: How are things going in the enforcement division?
Kapust: Well, enforcement is the cornerstone of the agency’s mission to ensure employers provide safe and healthful workplaces for their employees and remains a strong component – along with compliance assistance and education – of our balanced approach to workplace injuries and illnesses.
S+H: During an April 3 appropriations hearing, then-Secretary of Labor R. Alexander Acosta said he expects the number of OSHA inspections to increase when recently hired inspectors get up to speed. What does OSHA consider a reasonable time frame for new inspectors to be ready to go into the field on their own?
Kapust: Because there is a lot of variety – variations in previous experience, education and training – there is no specific time frame in which new [compliance safety and health officers], or compliance officers, are expected to be able to conduct inspections. However, the new staff generally begins shadowing veteran CSHOs as soon as possible, then progress to less complex assignments on their own within the first year.
S+H: OSHA is reportedly increasing its use of drones in inspections. How might it affect the Top 10?
Kapust: OSHA issued a memorandum to our regional administrators that presents a uniform protocol for the use of unmanned aircraft during enforcement activities. Most importantly, use of unmanned aircraft is generally limited to situations when it’s dangerous for site personnel and/or compliance officers to access areas for inspection. For example, drilling rigs, drilling rig explosions, storage tank collapse, things of that nature. And all parties agree to their use. Although there will not be a foreseeable impact on the Top 10 by the use of unmanned aircraft, OSHA does use them to conduct inspections more efficiently and with greater safety.
S+H: The Top 10 list shows that the occupational safety community has had to tackle many of the same problems or teach many of the same lessons year after year. What could help change that?
Kapust: From OSHA’s perspective, targeted enforcement and outreach are two critical tools in getting employers to identify and correct hazards in the workplace. Occupational safety and health professionals are encouraged to continue in their systematic approach of developing and promoting strong safety and health programs. OSHA’s Directorate of Training and Education, along with our occupational Training Institute Education Center partners, is a resource for educating and training employers and workers in safety awareness. OSHA’s cooperative programs are excellent ways for employers, employees and associations to work with OSHA on meaningful safety and health initiatives.
S+H: In what ways is the agency succeeding in fulfilling its core priorities?
Kapust: Our common goal is that every employee goes home safe and healthy at the end of the day. The agency is committed to maintaining a balanced approach to reaching this goal through compliance assistance and enforcement. Ensuring employers comply with OSHA standards is key to protecting employees. The possibility of an OSHA inspection and citations serves to deter employers who are not focused on their responsibilities to provide safe and healthful working conditions, as required by the OSH Act of 1970. Through our compliance efforts, OSHA has saved thousands of lives and prevented millions of injuries. Strong, fair, effective enforcement also levels the playing field between those employers who fulfill their responsibilities to provide safe workplaces and those employers who compete unfairly by putting their employees at risk of injury, illness or death. Emphasis programs play a very important role in accomplishing the mission of the agency. Just to highlight a few, OSHA reintroduced the Site-Specific Targeting Program utilizing employer-submitted injury and illness data from the 300A forms in calendar year 2016. SST inspections are identifying and ensuring abatement for serious hazards involving lockout/tagout, electricity, amputations, powered industrial trucks and hazard communication. OSHA revised the National Emphasis Program for trenching and excavation to address the disturbing upward trend of fatalities in excavation. One of OSHA’s goals regarding the emphasis program is to increase abated hazards found under that program. Each of these emphasis programs – and ones that exist that I did not mention – is effectively finding and collecting abatement for hazards to which employees are exposed. Other programs OSHA tries to utilize to meet the mission include the Severe Violator Enforcement Program, corporatewide settlement agreements, federal targeting programs for federal agencies and the Construction Targeting Program.
S+H: You joined OSHA nearly 30 years ago, in 1991. What are a few key takeaways and advancements you’ve observed? How do these influence your work today?
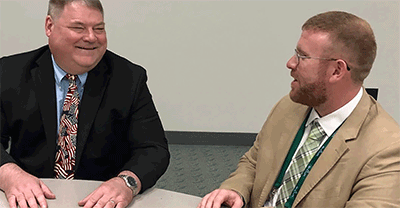
Patrick Kapust (left), deputy director of OSHA’s Directorate of Enforcement Programs, with Safety+Health Associate Editor Kevin Druley (right)
S+H: Anything else you’d like Safety+Health readers to know?
Kapust: Like I’ve always said, I think that the Top 10 cited hazards are a good place to start when looking for hazards in your own workplace. But it’s important for everyone to remember that a good safety and health program will have a long-term impact on your worksite’s overall safety and health performance. OSHA can help with that through the agency’s cooperative programs and the vast array of outreach materials on our website.
Post a comment to this article
Safety+Health welcomes comments that promote respectful dialogue. Please stay on topic. Comments that contain personal attacks, profanity or abusive language – or those aggressively promoting products or services – will be removed. We reserve the right to determine which comments violate our comment policy. (Anonymous comments are welcome; merely skip the “name” field in the comment box. An email address is required but will not be included with your comment.)