A collaborative approach to safety
ATS is the 2023 recipient of the Robert W. Campbell Award

A food processing facility in one instance. An aerospace components plant the next. Technicians and other team members at Peoria, IL-based industrial services provider Advanced Technology Services seldom operate in consistent environments.
ATS navigates that reality with a flexible, collaborative safety approach that focuses on employees’ overall well-being.
It has proved instrumental: The company is the 2023 recipient of the prestigious Robert W. Campbell Award – a National Safety Council honor presented to organizations that successfully integrate environmental, health and safety management with business operations.
“We do not have a standard approach to every single situation, because when something is broken or out of process, it’s not standard any longer,” said Rob Carbone, vice president of operations at ATS. “So, the amount of effort put in, the focus on looking out for one another, the observations by our leaders on the floor in real time – those are things that I think contribute to the success there, help us manage the risk. It’s really the engaging of our team on the floor.”
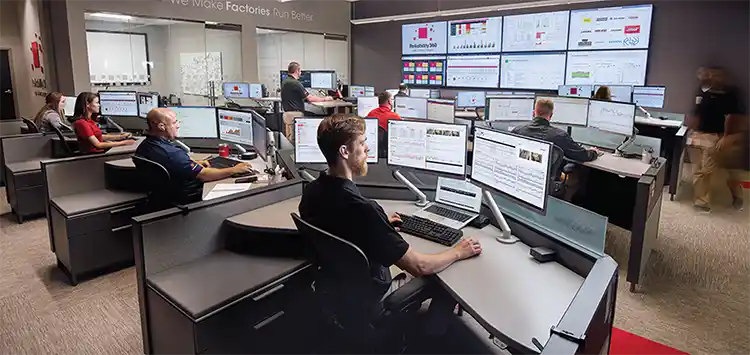
Advanced Technology Services has more than 2,800 employees across the United States, Mexico and the United Kingdom.
ATS observed a 9.2% reduction in its global recordable injury rate from 2021 to 2022, the company says. In addition, 70 of 91 ATS sites had zero recordable incidents in 2023, while 10 sites have gone at least a decade since their most recent incident.
To company leadership, the adaptive nature of ATS’ work – spread among more than 2,800 employees across the United States, Mexico and the United Kingdom – underscores the accomplishment.
Katherine Mendoza, director of the Campbell Institute and senior director of workplace programs at NSC, was also impressed by ATS’ acumen for risk management amid an ever-changing field.
“Their employees are armed with tools to identify hazards before each job and control those risks that are as dynamic as the job,” she said.
Staying diligent
ATS CEO Jeff Owens joined the company as a sales representative in 1988. Carbone came aboard as a maintenance technician 13 years later.
Their respective rises in rank have presented several lessons to the duo, but one stands out:
“Our world is totally nonroutine,” Owens said.
ATS built its safety program with that outlook in mind. ATS supervisors and team members recognize that each job has its own unique set of hazards, so they remain flexible when approaching tasks.
“Step back. Take your time. Look at the situation,” Owens said. “If you need to consult with a co-worker about, ‘Let’s double-check and think through this,’ about ‘What’s zero-energy?’ or ‘How do we lock this out properly?’ – make sure you do that. When you walk up to that machine, take a pause, take a breath, take in all the surroundings and understand what you’re getting yourself into.”
Through its Beyond Zero initiative, ATS encourages and empowers team members to “live safety” both on and off the job.
In addition to “the Live Safety 24/7 mindset,” Beyond Zero comprises four other elements: financial, physical, social and emotional well-being. Going a step further, ATS offers its employees and their families resources and tools that support each element.
“It’s keeping that conversation going about safety, about making sure they feel comfortable,” ATS Senior Director of EHS David Miller said. “To have the discussion when they don’t feel that things are safe.”
He added: “If you focus solely on OSHA and minimum compliance, that’s all you’re going to get. You’re not going to get that caring process.”
A ‘naturally embedded’ part of ATS
ATS was a previous finalist for the Campbell Award. Owens, who in 2021 was named one of NSC’s CEOs Who “Get It,” lauded the Campbell team’s onsite visits during the award’s evaluation processes.
The team’s collective interviews and interactions with management, supervisors and team members helped ATS recognize areas of growth in its EHS and company culture.
“They came and met with us, took us seriously, talked to us, helped us improve,” Owens said. “I mean, that, to me, is the way business in our society should work – helping each other, sharing best practices, being open and transparent. I got the sense from them that they truly cared about us and were helping us get better.”
ATS strives to make its employees feel the same way. Carbone, Miller and Owens each stressed the company’s cultural objectives of promoting teamwork and continuous improvement to achieve the common goal of improving manufacturing operations.
“Communicating and embracing everybody and getting their hearts engaged in this subject, watching out for each other, believing in it,” Owens said. “I think if you’re going to go to the highest level, just having the technical skill of safety, there’s no way you’re going to go to the top. It has to be an emotional, heartfelt, sincere, naturally embedded part of you, part of the company.”
Post a comment to this article
Safety+Health welcomes comments that promote respectful dialogue. Please stay on topic. Comments that contain personal attacks, profanity or abusive language – or those aggressively promoting products or services – will be removed. We reserve the right to determine which comments violate our comment policy. (Anonymous comments are welcome; merely skip the “name” field in the comment box. An email address is required but will not be included with your comment.)